Carburizing and quenching is actually a composite process, namely carburizing + quenching. We are often used to talk about the two together, because the two processes that are completed on the same equipment are the most commonly encountered in production (but there are also carburizing air cooling, carburizing slow cooling and then reheating and quenching processes, and secondary quenching. Process) Then some of the undesirable phenomena encountered in production are carburizing problems, some are quenching problems, and some are the result of the combined effects of carburizing and quenching.
We know that all heat treatment processes are inseparable from three core issues: heating, heat preservation, and cooling. In detail, including heating temperature, heating rate, holding time, cooling rate, and of course, atmosphere issues. So once something goes wrong, we will habitually analyze the cause from these aspects.
For carburizing and quenching, we often test these indicators: product surface appearance, surface hardness, core hardness, carburized layer depth, (effective hardened layer depth, fully hardened layer depth) metallographic structure, and deformation. Let’s share my views on these indicators respectively.
1. Appearance problem
1. Oxide scale: This is mainly due to equipment leakage, impure carrier gas, or water content. Need to find the reason from the equipment and raw materials.
2. The other most troublesome problem is the problem of stains, which is also a new and challenging requirement for heat treatment in modern times. The reasons are complicated and very profound.
two. Unqualified hardness
1. High hardness (not discussed)
2. Low hardness: There are two situations, one is unqualified carburizing. The reason may be that the carburized layer is too shallow to meet the requirements of the drawings, (the carburized layer is not infiltrated), or the selected detection scale exceeds the existing carburized layer tolerable range, which will break down the carburized layer.
Solution: Replenish the seepage and follow the inspection ruler. JBT 6050-2006 “General Principles for Heat Treatment Hardness Inspection of Steel Parts” The depth of the carburized layer is actually a function of temperature, time, and carbon potential. From the above factors, we can consider ways to increase the heating temperature, extend the holding time, and increase the carburizing potential. (Of course, the adjustment of each parameter should be fully combined with the requirements of your own equipment and products) It may also be because of the existence of non-horse organizations on the surface. Another situation occurs when the hardness is low, that is, the carburizing is qualified, but the quenching is unqualified. Generally speaking, it is not quenched. This situation is the most complicated, as the saying goes: heat treatment relies on heating for three quarters, and cooling for seven quarters. It also reflects the position that the cooling process occupies in the heat treatment process.
The following is a comparative test I designed. You can discuss the effect of cooling on hardness.
Take 3 groups of test bars with different materials but the same specifications and dimensions, the size of which is Φ20mmX100mm. (We call No. 20 steel test bar No. 1, 20Cr test bar No. 2 and 20CrMnTi test bar No. 3) The test bars are carburized in the same heat using the same process. Assuming that the carburized layer depth of the three test bars is 0.6-0.7mm (ps: the assumption is only established in an ideal state).
Please consider the following conditions:
a. Finish quenching under the same conditions
b. Quenching medium is slow oil, fast oil, clear water, salt water
c. In the same medium without stirring and intensively stirring and quenching, the three test bars are each taken in two groups for testing.
After the carburizing is completed, the A group is quenched at 800 degrees, and the B group is quenched at 860 degrees. What is the order of their hardness from high to low? How to order the hardened layer (with 550HV1.0 as the limit) from deep to shallow? Take two test bars of the same material and compare and test, which group can obtain higher quenching hardness and effective hardened layer depth?
Can it be concluded from the above test results that the depth of the carburized layer is not equal to the depth of the effective hardened layer, and the actual hardened layer depth is affected by the hardenability of the material, the quenching temperature, and the cooling rate. The cooling characteristics and quenching intensity of the cooling medium also affect the quenching effect. The above are people’s views, if there is any incompleteness, you can add. Of course, the size effect of the parts also affects the hardening effect.
I think an experienced inspector can determine the real cause of the low hardness by organizing and combining other testing methods, and then find the real cause to solve it; as a craftsman, if you are familiar with the characteristics of conventional metal raw materials, The cooling performance of its own equipment and medium have reached a certain level of recognition, which is of great help to the formulation of carburizing and quenching processes.
3. Uneven hardness: uniform furnace temperature (affecting carburizing uniformity), equipment structure, atmosphere circulation, furnace loading, (affecting uniformity of carburizing layer, and at the same time affecting quenching uniformity)
4. The core hardness is unqualified. Too high: the quenching temperature is too high, the hardenability of the material is too good, the upper limit of carbon and alloy composition, and the medium cooling rate is too fast. The core hardness is low: just the opposite.
Example sharing: 20# steel 1.5mm product, requirements: infiltration layer 0.2-0.4mm core HV250, some friends in the same industry think that the requirements are unreasonable, (everyone should know that the highest hardness of 20# steel slab martensite will be HV450- 470) To solve this problem, we must first understand the characteristics of this material: including hardenability and hardenability.
Then combine the above-mentioned factors that affect the quenching effect, and find ways to heat and cool. In this case, the material is fixed. We can figure out a way from the quenching temperature and cooling rate. This manufacturer happens to use over-speed oil. If reducing the quenching intensity does not meet the requirements, we can also reduce the quenching temperature. Method.
Still the same sentence, from 860-760 degrees, (when the temperature is lowered to a certain level, a certain amount of ferrite will be precipitated from the supercooled austenite in the core, and the hardness will decrease at this time. , The more the temperature decreases, the more the amount of ferrite precipitated, the more the hardness decreases.
Here is a reminder: It is necessary to fully combine the existing conditions of the equipment and make a fuss about the special favorable index of shallow permeability.
3. The carburized layer or effective carburized layer is deeper and shallower
As mentioned earlier, the depth of the infiltration layer is a comprehensive function of temperature, time, and carbon concentration. To solve this problem, we have to start with heating temperature, heating speed, holding time, cooling speed, and controlling the carbon concentration gradient in the carbon layer. The higher the temperature, the longer the time, and the higher the carbon potential, the deeper the infiltration layer, and vice versa.
But in fact, it is far more than that simple. To design a carburizing process, you must also consider the equipment, furnace capacity, oil characteristics, metallographic structure, material hardenability, the carbon concentration gradient in the carburized layer and the cooling rate. And many other factors. This can be analyzed with reference to the previous low hardness situation, and will not be explained in depth.
Fourth, metallographic organization
Excessive martensite: the raw material has coarse grains, or is not normalized, and the carburizing temperature is too high. Solution: normalizing or multiple normalizing, (it is recommended that the normalizing temperature is 20-30 degrees higher than the carburizing temperature) If possible, consider carburizing and slow cooling and then reheating and quenching
Excessive Paralympic: the quenching temperature is too high, the carbon content in the austenite is too high (the carbon potential is too high). Solution: Full diffusion and conditions permit can reduce the quenching temperature, high temperature tempering and reheating and quenching, or cryogenic treatment.
Excessive carbide: too high carbon content in austenite (too high carbon potential), too slow cooling process, carbide precipitation
Solution: fully diffuse, control the cooling rate, reduce the temperature difference between carburizing and quenching as possible, and use low temperature or sub-temperature quenching as little as possible. If this process must be used, the furnace load must be controlled. Let’s imagine: the same equipment is carburized at 920°C and quenched at 820°C. The furnace capacity is 1000kg and 600kg, and the cooling rate is the same? Which one will take longer? Which carbide grade is higher?
Fives. Non-horse and internal oxidation
Internal oxidation: It is the reaction between alloying elements such as chromium, manganese and molybdenum in the steel and the oxidizing atmosphere in the atmosphere (mainly oxygen, water, carbon dioxide), which depletes the alloying elements in the matrix, resulting in a decrease in the hardenability of the material. The black network structure can be seen under the microscope, its essence is the troostite structure obtained by the depletion of alloying elements in the matrix and the decrease of hardenability.
The solution is to find ways to increase the cooling rate of the medium, enhance the quenching intensity, and reduce the oxidizing atmosphere in the furnace (ensure the purity of the carburizing raw and auxiliary materials, minimize the amount of balanced air, control the balanced air moisture content, and ensure that the equipment does not leak. Sufficient exhaust) Conventional equipment is difficult to eliminate. It is said that the low-pressure vacuum carburizing equipment can be completely eliminated. In addition, powerful shot peening can also reduce the internal oxidation level.
I have read the opinions of some experts, and some believe that excessive ammonia in the carbonitriding process can also cause serious non-horseness. I personally have a different opinion on this: maybe it is caused by excessive water content in ammonia? Because I have been exposed to many carbonitriding processes, no obvious non-horse tissue was found when inspecting the product. (But I don’t think this view is wrong) Some foreign machinery industries attach great importance to internal oxidation, especially the gear industry. Domestically, the depth is generally required to be no more than 0.02mm as qualified.
Non-martensitic: non-martensitic structure appears on the surface of the carburized layer due to carburization or quenching problems after quenching, such as ferrite, bainite, and of course, internal oxidation type troostite. The generation mechanism is similar to internal oxidation, and the solution is similar.
Six. Deformation problem
This is a system problem, and it is also the most troublesome problem for our staff engaged in heat treatment. It is guaranteed from several aspects of raw material process cooling medium. The above content is only a personal experience. If there is any inconsistency, you are welcome to correct me, thank you.
Please keep the source and address of this article for reprinting:Collection of common defects and preventive measures in carburizing and quenching
Minghe Die Casting Company are dedicated to manufacture and provide quality and high performance Casting Parts(metal Die Casting parts range mainly include Thin-Wall Die Casting,Hot Chamber Die Casting,Cold Chamber Die Casting),Round Service(Die Casting Service,Cnc Machining,Mold Making,Surface Treatment).Any custom Aluminum die casting, magnesium or Zamak/zinc die casting and other castings requirements are welcome to contact us.
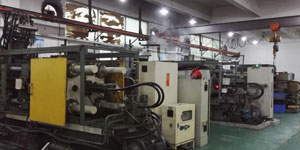
Under the control of ISO9001 and TS 16949,All processes are carried out through hundreds of advanced die casting machines, 5-axis machines, and other facilities, ranging from blasters to Ultra Sonic washing machines.Minghe not only has advanced equipment but also have professional team of experienced engineers,operators and inspectors to make the customer’s design come true.

Contract manufacturer of die castings. Capabilities include cold chamber aluminum die casting parts from 0.15 lbs. to 6 lbs., quick change set up, and machining. Value-added services include polishing, vibrating, deburring, shot blasting, painting, plating, coating, assembly, and tooling. Materials worked with include alloys such as 360, 380, 383, and 413.
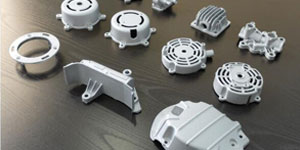
Zinc die casting design assistance/concurrent engineering services. Custom manufacturer of precision zinc die castings. Miniature castings, high pressure die castings, multi-slide Mold castings, conventional mold castings, unit die and independent die castings and cavity sealed castings can be manufactured. Castings can be manufactured in lengths and widths up to 24 in. in +/-0.0005 in. tolerance.
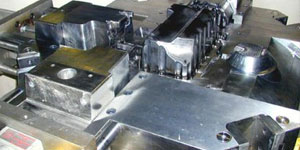
ISO 9001: 2015 certified manufacturer of die cast magnesium, Capabilities include high-pressure magnesium die casting up to 200 ton hot chamber & 3000 ton cold chamber, tooling design, polishing, molding, machining, powder & liquid painting, full QA with CMM capabilities, assembly, packaging & delivery.
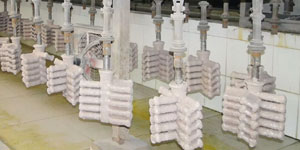
ITAF16949 certified. Additional Casting Service Include investment casting,sand casting,Gravity Casting, Lost Foam Casting,Centrifugal Casting,Vacuum Casting,Permanent Mold Casting,.Capabilities include EDI, engineering assistance, solid modeling and secondary processing.
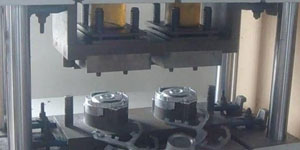
Casting Industries Parts Case Studies for: Cars, Bikes, Aircraft, Musical instruments, Watercraft, Optical devices, Sensors, Models, Electronic devices, Enclosures, Clocks, Machinery, Engines, Furniture, Jewelry, Jigs, Telecom, Lighting, Medical devices, Photographic devices, Robots, Sculptures, Sound equipment, Sporting equipment, Tooling, Toys and more.
What Can we help you do next?
∇ Go To Homepage For Die Casting China
→Casting Parts-Find out what we have done.
→Ralated Tips About Die Casting Services
By Minghe Die Casting Manufacturer |Categories: Helpful Articles |Material Tags: Aluminum Casting, Zinc Casting, Magnesium Casting, Titanium Casting, Stainless Steel Casting, Brass Casting,Bronze Casting,Casting Video,Company History,Aluminum Die Casting |Comments Off
Please keep the source and address of this article for reprinting:Collection of common defects and preventive measures in carburizing and quenching
Reprint Statement: If there are no special instructions, all articles on this site are original. Please indicate the source for reprinting.:Cnc Machine Wiki,Thanks!^^