EDM (abbreviated as EDM, full name Electrical Discharge Machining) is a kind of machining equipment, mainly used for EDM. It is widely used in the manufacture of various metal molds and mechanical equipment. It is a special processing method that uses the electro-corrosion effect generated during the pulse discharge between the two electrodes immersed in the working fluid to etch away conductive materials, also known as electrical discharge machining or electro-erosion machining.
Spark machining is mainly used for processing molds and parts with complex shaped holes and cavities; processing various conductive materials, such as cemented carbide and quenched steel, etc.; processing deep and thin holes, special-shaped holes, deep grooves, narrow slits and Cutting thin slices, etc.; processing various forming tools, templates and thread ring gauges and other tools.
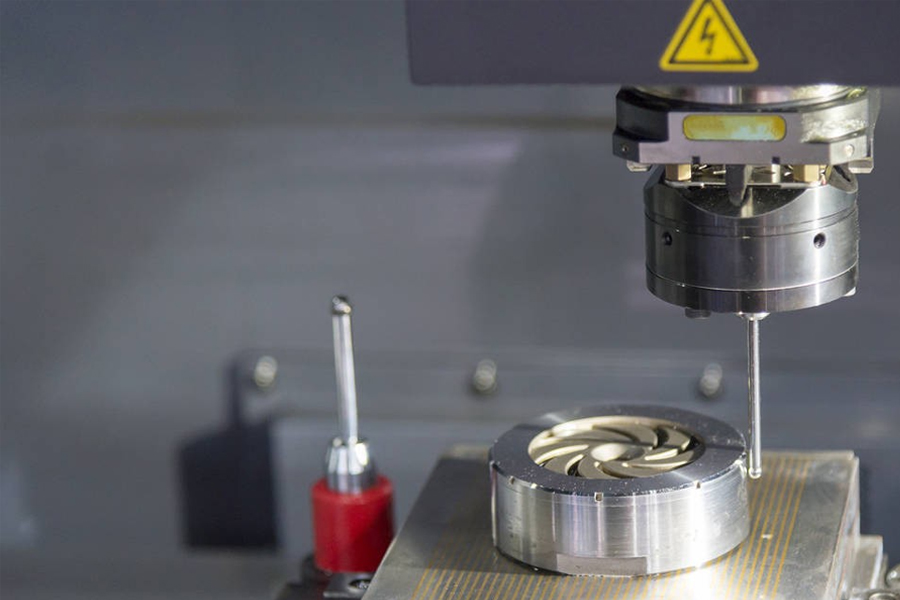
edm
List of Contents
The Processing Principle Of EDM
When performing EDM, the tool electrode and the workpiece are respectively connected to the two poles of the pulse power supply and immersed in the working fluid, or the working fluid is charged into the discharge gap. Through the gap automatic control system, the tool electrode is controlled to feed to the workpiece. When the gap between the two electrodes reaches a certain distance, the pulse voltage applied on the two electrodes will break down the working fluid and generate spark discharge.
A large amount of heat energy is instantaneously concentrated in the micro-channel of the discharge, the temperature can be as high as 10000℃, and the pressure also changes sharply, so that the small amount of metal material on the working surface at this point is immediately melted, vaporized, and exploded into the working fluid. , Rapidly condenses, forming solid metal particles, which are taken away by the working fluid. At this time, a tiny pit mark is left on the surface of the workpiece, the discharge is temporarily suspended, and the working fluid between the two electrodes restores the insulation state.
Immediately afterwards, the next pulse voltage breaks down at another point relatively close to the two electrodes, generating a spark discharge, and repeating the above process. In this way, although the amount of metal eroded by each pulse discharge is very small, because there are thousands of pulse discharges per second, more metals can be eroded, which has a certain productivity.
Under the condition of maintaining a constant discharge gap between the tool electrode and the workpiece, while eroding the workpiece metal, the tool electrode is continuously fed to the workpiece, and finally a shape corresponding to the shape of the tool electrode is processed. Therefore, as long as the shape of the tool electrode and the relative movement between the tool electrode and the workpiece are changed, various complex profiles can be processed. Tool electrodes are commonly used electro-corrosion-resistant materials with good conductivity, high melting point, and easy processing, such as copper, graphite, copper-tungsten alloy, and molybdenum. During the machining process, the tool electrode is also lost, but it is less than the amount of metal erosion of the workpiece, and even close to no loss.
As the discharge medium, the working fluid also plays a role in cooling and chip removal during processing. Commonly used working fluids are media with low viscosity, high flash point and stable performance, such as kerosene, deionized water and emulsion. EDM is a kind of self-excited discharge, and its characteristics are as follows: The two electrodes of spark discharge have a higher voltage before discharge. When the two electrodes are close, after the medium between them is broken down, spark discharge occurs immediately. With the breakdown process, the resistance between the two electrodes decreases sharply, and the voltage between the two electrodes also decreases sharply. The spark channel must be extinguished in time after a short period of time (usually 10-7-10-3s) in order to maintain the “cold pole” characteristics of spark discharge (that is, the heat energy converted by the channel energy cannot be transmitted to the depth of the electrode). The channel energy acts on a very small area. The effect of channel energy can cause the electrode to be corroded locally.
The method of sizing materials by using the corrosion phenomenon generated during spark discharge is called EDM. EDM is the spark discharge in the liquid medium in the lower voltage range. According to the form of the tool electrode and the characteristics of the relative movement between the tool electrode and the workpiece, the EDM machining can be divided into five categories: the use of the forming tool electrode and the EDM processing with a simple feed motion relative to the workpiece; Axial-moving metal wire is used as tool electrode, and the workpiece is moved according to the required shape and size for wire EDM cutting of conductive materials; metal wire or shaped conductive grinding wheel is used as tool electrode for small hole grinding or forming EDM grinding for grinding; EDM conjugate rotary machining for machining threaded ring gauges, threaded plug gauges, gears, etc.; small hole machining, engraved surface alloying, surface strengthening and other types of machining. EDM can process materials and complex-shaped workpieces that are difficult to cut by ordinary cutting methods; there is no cutting force during processing; no defects such as burrs and tool marks and grooves are generated; the tool electrode material does not need to be harder than the workpiece material; it is easy to use electrical energy for processing Realization of automation; a metamorphic layer is generated on the surface after processing, which must be further removed in some applications; the purification of working fluid and the treatment of smoke pollution generated during processing are more troublesome.
The Development Process Of EDM
In 1943, Soviet scholars Lazarenko and his wife researched and invented electric discharge machining, and then developed rapidly with the improvement of pulse power supply and control system. The first pulse power used was a simple resistor-capacitor circuit. In the early 1950s, it was improved into a circuit such as resistance-inductance-capacitance. At the same time, so-called long-pulse power supplies such as pulse generators are also used to improve the erosion efficiency and reduce the relative wear of tool electrodes.
Then there appeared high-frequency pulse power supplies such as high-power electron tubes and thyratrons, which improved the productivity under the same surface roughness conditions. In the mid-1960s, transistors and thyristor pulse power sources appeared, which improved energy efficiency and reduced tool electrode loss, and expanded the adjustable range of rough and fine machining.
By the 1970s, power supplies such as high and low voltage composite pulses, multi-circuit pulses, constant amplitude pulses and adjustable waveform pulses appeared, and new progress was made in processing surface roughness, processing accuracy, and reducing tool electrode wear. In terms of the control system, from the initial simple maintenance of the discharge gap to control the advance and retreat of the tool electrode, it has gradually developed to the use of a microcomputer to timely control various factors such as electrical and non-electrical parameters.
The Species Of EDM
1.Mirror
The mirror spark machine is a spark machine that can process the mirror effect. It is the best spark machine today. The processed Mold can be directly used in production without saving molds, saving labor and improving efficiency. Moreover, the mirror The precision of the spark machine is high, especially in the application of precision molds. The cost of mirror spark machines is high. Imported mirror spark machines range from 700, 800,000 to one million as high as millions. In recent years, my country has also introduced mirror spark machines, all of which are joint ventures with foreign mirror spark machine manufacturers.
2.Electric discharge machine
Plastic Mold electric discharge machine is our more common spark machine, which is mainly used for electric discharge machining of plastic mold. It is relatively common in our country, cheap, widely used, and the average price is no more than 100,000.
3.Pore Discharge Machine
The pinhole electric discharge machine is also a kind of electric spark. Its main purpose is to punch holes in the mold.
4.other
For example, specializing in graphite, specializing in tungsten steel.
5.ZNC
ZNC spark machine Z axis numerical control, X axis and Y axis manual, it is a more practical spark machine!
6.CNC
The CNC spark machine has XYZ three-axis numerical control. The CNC spark machine has many functions such as automatic profiling, automatic centering, automatic programming, G code programming, and three-axis linkage discharge.
The Machine Characteristics Of EDM
Technical specifications
project
|
unit
|
SP1
|
SP2
|
HP35
|
HP45
|
Workbench size (length * width)
|
mm
|
600*400
|
600*400
|
650*450
|
800*500
|
X, Y, Z axis travel
|
mm
|
300*210*270
|
350*250*270
|
400*300*270
|
500*400*350
|
Maximum motor weight
|
kg
|
25
|
50
|
50
|
100
|
Maximum workpiece weight
|
kg
|
400
|
400
|
400
|
800
|
Work table to electrode
Minimum/maximum distance of the board
|
mm
|
295/565
|
330/600
|
350/620
|
368/718
|
Machine weight
CNC power supply
|
kg
|
2000
|
2200
|
2200
|
4000
|
Total input power
|
KVA
|
13
|
13
|
13
|
15
|
Performance Characteristics
- Adaptive electrical discharge machining control
- Timing high-speed tool lifting and tool lifting height control
- Spindle fixed-point control, discharge gap detection
- Oil level control
- Fire Control
- Automatic alarm safety device
- Anti-carbon deposition function
- CNC system, touch screen input, manual control box operation.
- The workpiece is automatically measured on the machine
- Super finishing
- Ultra-precision edge processing
- X, Y, Z axis imported Panasonic servo system.
- Stainless steel material wear-resistant edging design
- Minimum electrode loss 0.10%
- The best surface roughness Ra0.2um
- The highest production efficiency is 500 mm3/min (standard) 1000 mm3/min (optional)
- Minimum drive unit 1um
CNC Power Supply
- Touch screen 15 inch LCD liquid crystal display.
- USB data input and output.
- Mirror processing and special material processing circuits such as special hard alloy.
- Special circuit for high-speed graphite processing, AUTO processing function unit.
- Low loss loop, automatic positioning function unit.
- High-speed and high-precision processing system.
- Automatic detection circuit for preventing carbon deposition and automatic arc cleaning circuit unit.
- Expert process database system.
- CNC instruction, standard G code, ISO code.
- Power-off reset, error message prompt function.
Direction Of Development
The spark machine is also known as the electric spark forming machine. The future development of the three-axis linkage numerical control is the forward direction, such as CNC electric spark, and the spark machine is refined, the spark machine is intelligent, the spark machine is automated, and the spark machine is highly efficient.
Precision
The core of EDM machining is mainly reflected in the requirements for dimensional accuracy, profiling accuracy, and surface quality. By adopting some advanced processing technologies, the mirror processing effect can be achieved and the EDM processing of high-precision mold parts such as micro connectors, IC plastic packaging, mobile phones, CD boxes, etc. can be successfully completed. Therefore, the electric discharge machine comprehensively promotes the further development of the existing Cnc Machining technology, and continuously improves the machining accuracy of the mold.
The Maintenance Of EDM
Daily maintenance
- Keep the work surface of the spark machine clean, if improperly, it may cause the surface to rust.
- Confirm whether the oil pump pressure is normal.
- Keep the appearance of the equipment clean and tidy.
Weekly maintenance
- Fill the oil with the hand-type lubricator, press 3 times each time.
- Check the amount of oil in the hand-operated lubricator.
Monthly maintenance
- Grease each guide rail of the spark machine.
- Check the disk accuracy. (Check whether the flatness is correct with a dial indicator)
Maintenance every season
- Check whether the spark machine level is normal. (Use a spirit level to measure whether the level of the work surface is correct)
- Check the accuracy of the three-axis of the spark machine. (Measure whether the stroke is correct by the pitch gauge)
Annual maintenance
- Check and clean the spark engine oil tank.
- Check and replace the Z-axis lubricant of the spark machine. (For details, please contact Qunji Service Department)
- Check and clean the electrical cabinet. (For details, please contact Qunji Service Department)
Regarding filter, filter cotton, sparking oil, etc., it is related to the frequency of use and the amount of erosion. It is recommended to check every six months and confirm whether to replace it according to the actual situation.
- Intelligentization: The spark machine adopts intelligent control technology. The intelligence of EDM is embodied in two aspects: precise detection technology and fuzzy control technology. Online automatic monitoring and adjustment of the processing process to achieve the most optimized control of the processing process. Fuzzy control technology is to determine the state of the EDM gap by computer monitoring, and automatically select the processing conditions that maximize the processing efficiency within the range of maintaining a stable arc.
- Automation: When the spark machine is equipped with an electrode library and a standard electrode fixture, as long as the electrode is loaded into the tool library before machining and the machining program is compiled, the entire EDM process can run automatically day after day, almost no need Manual operation. The automatic operation of the machine tool reduces the labor intensity of the operator and improves the production efficiency. The automatic measurement and alignment, automatic positioning, continuous processing of multiple workpieces and other functions of the spark machine have given full play to its automation performance. The automatic operation process does not require manual intervention, which can improve the processing accuracy and efficiency.
- High efficiency: EDM greatly improves the efficiency of rough and finish machining under the premise of ensuring machining accuracy. Fields such as mobile phone shells, home appliances, electrical appliances, and electronic meters all require the discharge time of large-area workpieces to be drastically shortened while reducing the roughness. After discharging, manual polishing is unnecessary. This not only shortens the processing time and saves the trouble of post-processing, but also improves the quality of the mold. The use of spark machine powder processing can meet the requirements.
Please keep the source and address of this article for reprinting:EDM
Reprint Statement: If there are no special instructions, all articles on this site are original. Please indicate the source for reprinting.:Cnc Machine Wiki,Thanks!^^