cnc machine is the abbreviation of digital control machine tool, which is an automatic machine tool equipped with a program control system. The control system can logically process a program with a control code or other symbolic instructions, decode it, express it with coded numbers, and input it into the numerical control device through an information carrier. After arithmetic processing, the numerical control device sends out various control signals to control the action of the machine tool, and automatically process the parts according to the shape and size required by the drawing.
The CNC machine tool solves the problem of complex, precise, small batch, and multi-variety parts processing. It is a flexible, high-performance automatic machine tool, which represents the development direction of modern machine tool control technology, and is a typical electromechanical integration chemical products.
Main Features | Basic Composition | Technical Application | Machining Center |
Maintenance | Development History | Milling Cutter Selection | Power Requirements |
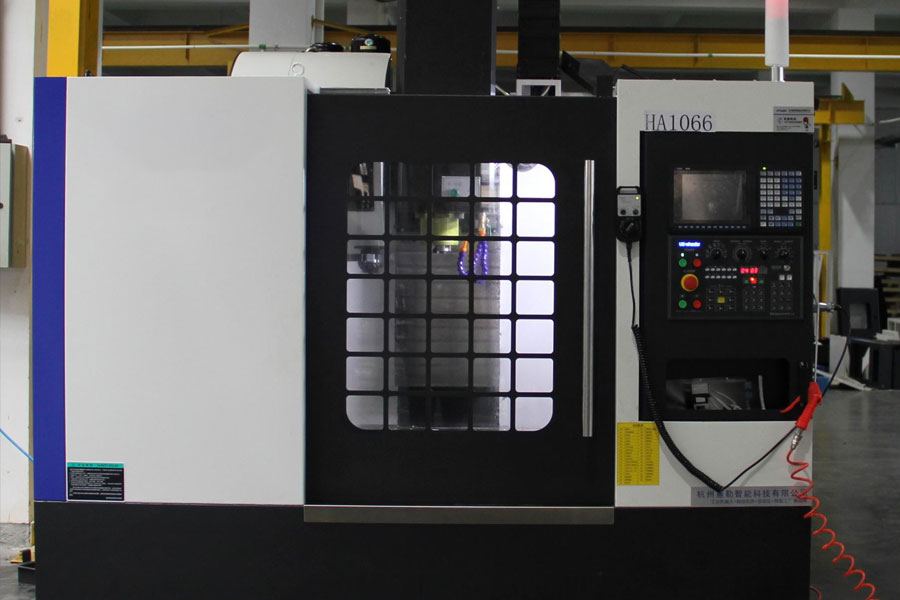
Cnc-MACHINE
The Main Features Of Cnc Machine
The operation and monitoring of the CNC machine tool are all completed in this CNC unit, which is the brain of the CNC machine tool. Compared with ordinary machine tools, CNC machine tools have the following characteristics:
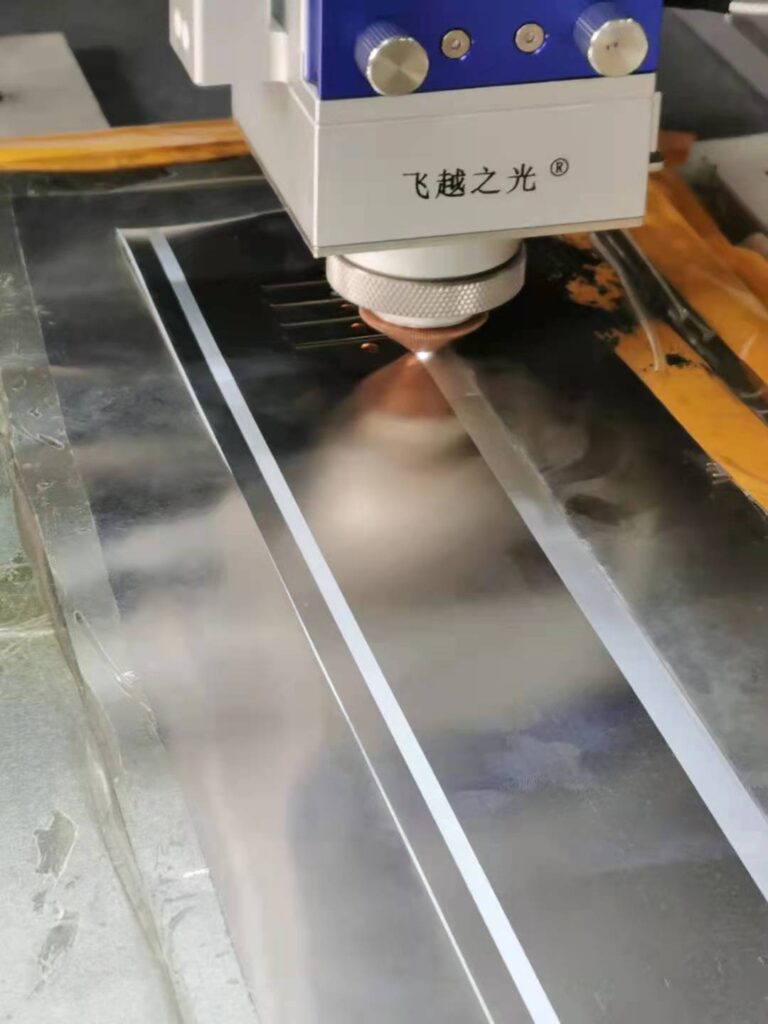
- It has strong adaptability to processing objects, adapts to the characteristics of single-piece production of products such as molds, and provides suitable processing methods for mold manufacturing;
- High processing precision and stable processing quality;
- Multi-coordinate linkage can be carried out, and parts with complex shapes can be processed;
- When machining parts change, generally only need to change the numerical control program, which can save production preparation time;
- The machine tool itself has high precision and high rigidity, can choose a favorable processing amount, and has high productivity (generally 3 to 5 times that of ordinary machine tools);
- The machine tool has a high degree of automation, which can reduce labor intensity;
- Conducive to the modernization of production management. CNC machine tools use digital information and standard codes to process and transmit information, and computer control methods are used to lay the foundation for the integration of computer-aided design, manufacturing and management;
- Higher requirements for the quality of operators and higher technical requirements for maintenance personnel;
- High reliability.
Compared with traditional machine tools, CNC machine tools have the following characteristics.
Highly Flexible
Machining parts on a CNC machine tool mainly depends on the processing program. It is different from ordinary machine tools. It does not need to be manufactured, many molds and fixtures are replaced, and the machine tool does not need to be re-adjusted frequently. Therefore, the Desktop CNC machine tool is suitable for the occasions where the processed parts are frequently replaced, that is, it is suitable for the production of single-piece, small-batch products and the development of new products, thereby shortening the production preparation cycle and saving a lot of process equipment costs.
High Processing Accuracy
The machining accuracy of CNC machine tools can generally reach 0.05-0.1mm. What Is Cnc Machine?CNC machine tools are controlled in the form of digital signals. Each time the CNC device outputs a pulse signal, the moving parts of the machine tool move a pulse equivalent (usually 0.001mm), and the machine tool advances The average error of the backlash of the transmission chain and the screw pitch can be compensated by the numerical control device. Therefore, the positioning accuracy of the numerical control machine tool is relatively high.
The Processing Quality Is Stable And Reliable
To process the same batch of parts, on the same machine tool, under the same processing conditions, using the same tool and processing procedure, the cutting path of the tool is exactly the same, the parts have good consistency, and the quality is stable.
High Productivity
The CNC machine tool can effectively reduce the processing time and auxiliary time of the parts. The range of the spindle sound speed and feed rate of the CNC machine tool is large, which allows the machine tool to perform powerful cutting with a large amount of cutting. CNC machine tools are entering the era of high-speed machining. The rapid movement and positioning of moving parts of CNC machine tools and high-speed cutting have greatly improved productivity. In addition, it can be used in conjunction with the tool magazine of the machining center to realize the continuous processing of multiple procedures on one machine tool, reducing the turnaround time of semi-finished products and improving productivity.
Improve Working Conditions
After the CNC machine tool is adjusted before processing, enter the program and start it, and the machine tool can automatically and continuously perform processing until the end of the processing. What the operator has to do is program input, editing, parts loading and unloading, tool preparation, processing state observation, and parts inspection. The labor intensity is greatly reduced, and the labor of machine tool operators tends to be intellectual work. In addition, machine tools are generally combined, which is both clean and safe.
Utilize Production Management Modernization
The processing of 3d CNC machine tools can accurately estimate the processing time in advance, standardize and modernize the tools and fixtures used, and it is easy to realize the standardization of processing information. It has been organically combined with computer-aided design and manufacturing (CAD/CAM). It is the foundation of modern integrated manufacturing technology
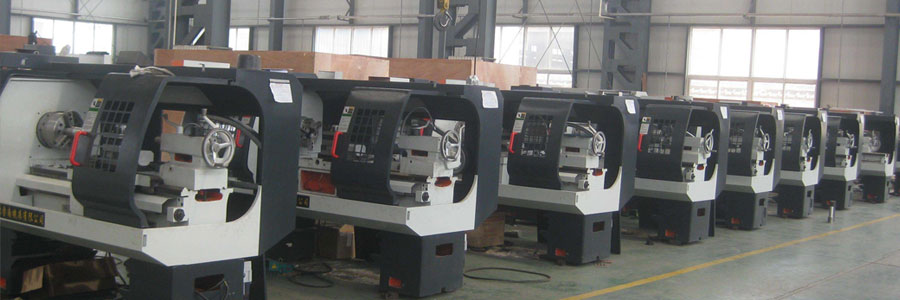
Basic Composition
Basic Composition
The basic composition of a CNC machine tool includes a processing program carrier, a CNC device, a servo drive device, the main body of the machine tool and other auxiliary devices. The basic working principles of each component are summarized below.
Processing program carrier
When the CNC machine tool is working, workers do not need to directly operate the machine tool. To control the CNC machine tool, it is necessary to compile a processing program. The part processing program includes the relative motion trajectory of the tool and the workpiece on the machine tool, the process parameters (feed amount, spindle speed, etc.), and auxiliary motion. The part processing program is stored in a program carrier with a certain format and code, such as punched tape, cassette tape, floppy disk, etc., and the program information is input to the CNC unit through the input device of the CNC Lathe machine tool.
CNC device
The numerical control device is the core of the numerical control machine tool. Modern numerical control devices all adopt the form of CNC (Computer Numerical Control). This kind of CNC device generally uses multiple microprocessors to realize numerical control functions in the form of programmed software, so it is also called Software NC (Software NC). CNC system is a kind of position control system, it is based on the input data to interpolate the ideal motion trajectory, and then output to the execution component to process the required parts. Therefore, the numerical control device is mainly composed of three basic parts: input, processing and output. And all these tasks are reasonably organized by the computer system program, so that the entire system can work in a coordinated manner.
1) Input device: Input the numerical control instruction to the numerical control device. According to the different program carrier, there are different input devices. There are mainly keyboard input, disk input, CAD/CAM system direct communication input and DNC (direct numerical control) input connected to a higher-level computer. There are still many systems that still retain the paper tape input form of photoelectric readers.
- (1) Paper tape input method. The part program can be read in with a paper tape photoelectric reader to directly control the movement of the machine tool, or the content of the paper tape can be read into the memory, and the part program stored in the memory can be used to control the motion of the machine tool.
- (2) MDI manual data input mode. The operator can use the keyboard on the operation panel to input the instructions of the processing program, which is suitable for relatively short programs.In the edit state of the control device (EDIT), use the software to input the processing program and store it in the memory of the control device. This input method can reuse the program. This method is generally used for manual programming.On the numerical control device with conversational programming function, you can select different menus according to the questions prompted on the display, use the method of man-machine dialogue, and input the relevant size numbers to automatically generate the processing program.
- (3) Adopt DNC direct numerical control input method. Save the part program in the upper-level computer, and the CNC system receives subsequent program segments from the computer while processing. The DNC method is mostly used when using CAD/CAM software to design complex workpieces and directly generate part programs.
2) Information processing: the input device transmits the processing information to the CNC unit and compiles it into information that can be recognized by the computer. The information processing part stores and processes it step by step in accordance with the regulations of the control program, and then sends position and speed commands to the servo through the output unit System and main motion control part. The input data of the CNC system includes: the contour information of the part (start point, end point, straight line, arc, etc.), processing speed and other auxiliary processing information (such as tool change, speed change, coolant switch, etc.). The purpose of data processing is to complete the insertion Preparations before the complement operation. The data processing program also includes tool radius compensation, speed calculation and processing of auxiliary functions.
3) Output device: The output device is connected with the servo mechanism. The output device receives the output pulse of the arithmetic unit according to the command of the controller, and sends it to the servo control system of each coordinate. After power amplification, the servo system is driven to control the machine tool to move as required.
Servo and measurement feedback system
Servo system is an important part of CNC machine tools, used to realize the feed servo control and spindle servo control of CNC machine tools. The function of the servo system is to convert the command information received from the numerical control device into the linear displacement or angular displacement motion of the execution parts of the machine tool after power amplification and shaping. Since the servo system is the last link of a CNC machine tool, its performance will directly affect the accuracy and speed of the CNC machine tool and other technical indicators. Therefore, the servo drive device of the Home CNC machine tool requires good fast response performance and accurate and sensitive tracking of the CNC device. The digital command signal sent out can faithfully execute the command from the numerical control device to improve the system’s dynamic following characteristics and static tracking accuracy.
The servo system includes two parts, the drive device and the actuator. The drive device is composed of a spindle drive unit, a feed drive unit, a spindle servo motor, and a feed servo motor. Stepping motors, DC servo motors and AC servo motors are commonly used driving devices.
The measuring element detects the actual displacement value of each coordinate 5 axis CNC machine tool and inputs it to the CNC device of the machine tool through the feedback system. The CNC device compares the feedback actual displacement value with the command value, and outputs to the servo system to reach the set value The required displacement command.
Machine body
The machine tool host is the main body of the CNC machine tool. It includes machine parts such as bed, base, column, beam, sliding seat, worktable, headstock, feed mechanism, tool post and automatic tool changer. It is a mechanical part that automatically completes various cutting processes on a CNC machine tool. Compared with traditional machine tools, the main body of CNC machine tools has the following structural characteristics:
- 1) Adopt a new machine tool structure with high rigidity, high shock resistance and less thermal deformation. Generally, methods such as improving the static stiffness of the structural system, increasing the damping, adjusting the quality of the structural parts and the natural frequency are used to improve the stiffness and seismic resistance of the machine tool host, so that the main body of the machine tool can adapt to the needs of CNC milling machine tools for continuous and automatic cutting. Taking measures such as improving the layout of the machine tool, reducing heat generation, controlling temperature rise, and adopting thermal displacement compensation, can reduce the impact of thermal deformation on the host machine of the machine tool.
- 2) The extensive use of high-performance spindle servo drive and feed servo drive devices shortens the transmission chain of CNC machine tools and simplifies the structure of the machine tool mechanical transmission system.
- 3) The use of high transmission efficiency, high precision, no gap transmission devices and moving parts, such as ball screw nut pairs, plastic sliding guides, linear rolling guides, static pressure guides, etc.
Numerically controlled machine tool auxiliary device
Auxiliary devices are necessary supporting devices to ensure full use of the functions of CNC machine tools. Commonly used auxiliary devices include: pneumatic, hydraulic devices, chip removal devices, cooling and lubricating devices, rotary table and CNC indexing head, protection, lighting, etc. assisting equipments.
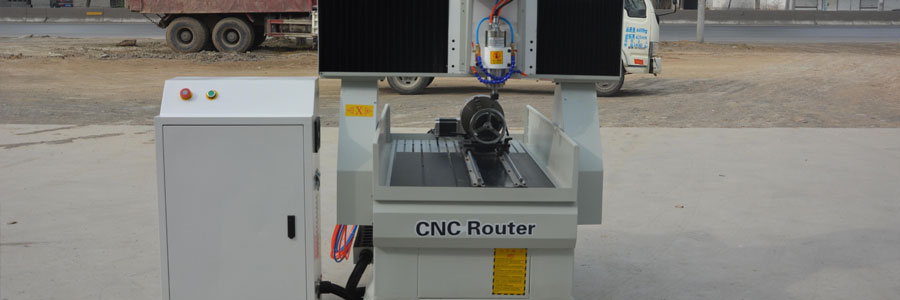
Cnc-Router-Machine
The Technical Application Of Cnc Machine
A CNC machine tool is an automated machine tool equipped with a program control system, which can make the machine tool move and process parts according to the programmed program. It integrates the latest technologies of machinery, automation, computer, measurement, microelectronics, etc., and uses a variety of sensors. The sensors used on CNC machine tools mainly include photoelectric encoders, linear gratings, proximity switches, temperature sensors, Hall sensors, and current Sensors, voltage sensors, pressure sensors, liquid level sensors, resolvers, induction synchronizers, speed sensors, etc., are mainly used to detect position, linear and angular displacement, speed, pressure, temperature, etc.
1. The requirements of CNC machine tools for sensors
- 1) High reliability and strong anti-interference;
- 2) Meet the requirements of accuracy and speed;
- 3) Easy to use and maintain, suitable for machine tool operating environment;
- 4) Low cost.
Different types of CNC machine tools have different requirements for sensors. Generally speaking, large-scale machine tools require high speed response, and medium-sized and high-precision wood CNC machine tools require precision.
2. Application of induction synchronizer
The induction synchronizer is made using the principle that the mutual inductance of two planar windings varies with different positions. Its function is to convert the angular or linear displacement into the phase or amplitude of the induced electromotive force, which can be used to measure the linear or angular displacement. According to its structure, it can be divided into linear type and rotary type. The linear induction synchronizer is composed of two parts: a fixed length and a sliding rule. The fixed length is installed on the machine bed, and the sliding rule is installed on the moving parts and moves with the worktable. The stator of the rotary induction synchronizer is a fixed disc, and the rotor For rotating discs. Induction synchronizer has the advantages of high accuracy and resolution, strong anti-interference ability, long service life, simple maintenance, long-distance displacement measurement, good manufacturability, and low cost. Rotary induction synchronizers are widely used in turntables of machine tools and instruments and various rotary servo control systems.
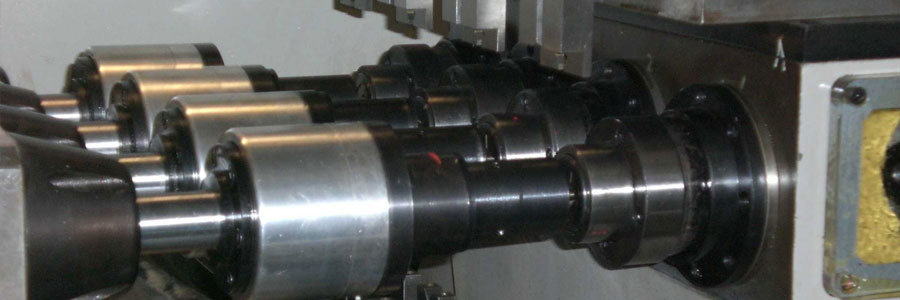
Machining Center
Machining Center
The first machining center was first developed by Carney-Trek in 1958. It adds an automatic tool changer on the basis of the CNC horizontal boring and milling machine, which realizes the centralized processing of multiple processes such as milling, drilling, boring, reaming, and tapping after the workpiece is clamped once.
The machining center is a highly automated multifunctional CNC machine tool with a tool magazine and an automatic tool changer. After the workpiece is clamped on the machining center once, multiple processes can be completed on more than two surfaces, and there are multiple tool change or tool selection functions, which greatly improves the production efficiency.
Machining centers are divided into boring and milling and turning according to their processing procedures, and can be divided into three-axis, four-axis and five-axis machining centers according to the number of control axes.
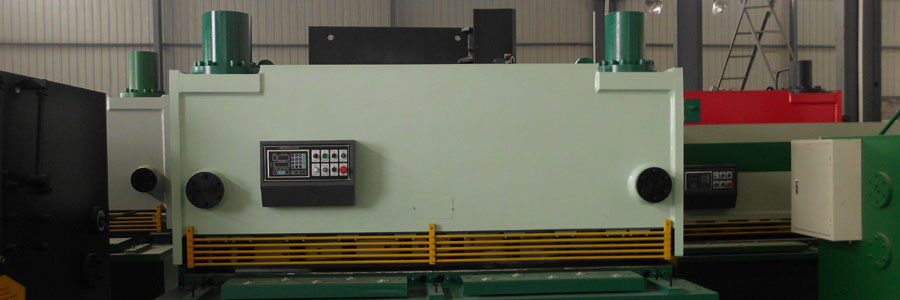
The Maintenance Of Cnc Machine
The Maintenance Of Cnc Machine
Extend the life of components and the wear cycle of parts, prevent various failures, and increase the average trouble-free working time and service life of CNC machine tools.
Use attention
- The use environment of CNC machine tools: For CNC machine tools, it is best to place them in a constant temperature environment and away from equipment with large vibrations (such as punching machines) and equipment with electromagnetic interference;
- Power requirements;
- Numerical control machine tools should have operating procedures: regular maintenance, maintenance, attention to record failures to protect the site, etc.;
- CNC machine tools are not suitable for long-term storage, as long-term storage system failures and data loss will be caused;
- Pay attention to training and equipping operators, maintenance personnel and programmers.
Maintain the constitution
Maintenance of CNC system
- Strictly abide by the operating procedures and daily maintenance system.
- Prevent dust from entering the numerical control device: Floating dust and metal powder can easily cause the insulation resistance between components to decrease, leading to failure or even damage to the components.
- Regularly clean the heat dissipation and ventilation system of the CNC cabinet.
- Frequently monitor the grid voltage of the numerical control system: the grid voltage range is 85% to 110% of the rated value.
- Regularly replace the storage battery.
- Maintenance of the numerical control system when it is not in use for a long time: often power on the numerical control system or allow the numerical control machine tool to run a warm machine program.
- Maintenance of spare circuit boards. Maintenance of mechanical parts.
Maintenance of mechanical parts
1. Maintenance of tool magazine and tool change manipulator
- 1) When manually loading the tool into the tool magazine, ensure that it is installed in place and check whether the locking on the tool holder is reliable;
- 2) It is strictly forbidden to load overweight and overlong tools into the tool magazine to prevent the tool from being dropped when the manipulator changes the tool or the tool collides with the workpiece, fixture, etc.;
- 3) When using sequential tool selection, pay attention to whether the order of the tools placed on the magazine is correct. Other tool selection methods should also pay attention to whether the number of the tool to be changed is consistent with the required tool to prevent accidents caused by changing the wrong tool;
- 4) Pay attention to keep the knife handle and knife sleeve clean;
- 5) Frequently check whether the zero return position of the tool magazine is correct, check whether the position of the machine spindle return tool change point is in place, and adjust it in time, otherwise the tool change action cannot be completed;
- 6) When starting up, the tool magazine and manipulator should be run dry first to check whether each part works normally, especially whether each travel switch and solenoid valve can operate normally.
2. Maintenance of ball screw pair
- 1) Regularly check and adjust the axial clearance of the screw nut pair to ensure the accuracy of the reverse transmission and the axial rigidity;
- 2) Regularly check whether the connection between the screw support and the bed is loose and whether the support bearing is damaged. If there are any of the above problems, tighten the loose parts in time and replace the support bearings;
- 3) For ball screws with grease, clean the old grease on the screw every six months and replace with new grease. The ball screw lubricated with lubricating oil should be refueled once a day before the machine tool works;
- 4) Take care to prevent hard dust or chips from entering the lead screw guard and hitting the guard during work. If the guard is damaged, it should be replaced in time.
3. Maintenance of the main drive chain
- 1) Regularly adjust the tightness of the spindle drive belt;
- 2) Prevent all kinds of impurities from entering the fuel tank. Change the lubricating oil once a year;
- 3) Keep the connecting part of the spindle and the tool holder clean. It is necessary to adjust the displacement of hydraulic cylinder and piston in time;
- 4) Adjust the counterweight in time.
4. Hydraulic system maintenance
- 1) Regularly filter or replace the oil;
- 2) Control the temperature of the oil in the hydraulic system;
- 3) Prevent leakage of hydraulic system;
- 4) Regularly check and clean the fuel tank and pipeline;
- 5) Implement the daily point inspection system.
5. Maintenance of pneumatic system
- 1) Remove impurities and moisture from compressed air;
- 2) Check the oil supply of the lubricator in the system;
- 3) Maintain the tightness of the system;
- 4) Pay attention to adjusting the working pressure;
- 5) Clean or replace pneumatic components and filter elements.
Troubleshooting
In CNC machine tools, most of the faults are available for investigation, but there are also some faults. The alarm information provided is vague or even no alarm at all, or the period of occurrence is long, irregular, and irregular, which brings to the search and analysis. Many difficulties. For such machine tool failures, it is necessary to analyze the specific conditions and perform patient search. In addition, comprehensive knowledge of machinery, electricity, hydraulics, etc. is particularly required during the inspection, otherwise it is difficult to quickly and correctly find the real cause of the failure.
Abnormal machining accuracy failures: system parameters change or change, mechanical failures, machine tool electrical parameters are not optimized, abnormal motor operation, abnormal machine tool position loops or incorrect control logic are common causes of abnormal machining accuracy failures of CNC machine tools in production, and find out related If the fault point is dealt with, the machine tool can return to normal. In production, we often encounter faults with abnormal machining accuracy of CNC machine tools. Such faults are highly concealed and difficult to diagnose.
There are five main reasons for this type of failure:
- 1. The feed unit of the machine tool is changed or changed;
- 2. The zero offset (NULLOFFSET) of each axis of the machine tool is abnormal;
- 3. The axial backlash (BACKLASH) is abnormal;
- 4. The motor running status is abnormal, that is, the electrical and control parts are faulty;
- 5. Mechanical failure, such as screw rod, bearing, shaft coupling and other parts.
In addition, the preparation of the processing program, the selection of tools and human factors may also cause abnormal processing accuracy.
If the machining accuracy is abnormal due to mechanical failure, the following aspects should be checked one by one.
- 1. Check the machining program segment that is running when the machine accuracy is abnormal, especially the calibration and calculation of tool length compensation and machining coordinate system (G54~G59).
- 2. In the jog mode, move the Z axis repeatedly, and diagnose the motion state by sight, touch, and listen. It is found that the sound of the Z-direction movement is abnormal, especially when the jog is fast, the noise is more obvious. Judging from this, there may be hidden dangers in machinery [1].
Malfunction Exclude
- 1. Initialization reset method: Under normal circumstances, system alarms caused by instantaneous faults can be cleared by hardware reset or switch system power in turn. If the system working storage area is lost due to power failure, unplugging the circuit board or battery undervoltage, it will cause confusion , The system must be initialized and cleared. Before clearing, you should make a record of data copy. If the fault cannot be eliminated after initialization, perform hardware diagnosis.
- 2. Parameter modification and program correction method: System parameters are the basis for determining system functions, and parameter setting errors may cause system failures or invalid functions. Sometimes due to user program errors can also cause failures to stop, this can be checked by the system’s block search function to correct all errors to ensure its normal operation.
- 3. Adjustment and optimization adjustment method: Adjustment is the simplest and most feasible method. Correct the system failure by adjusting the potentiometer. For example, during maintenance in a factory, the system display screen is chaotic, and it is normal after adjustment. For example, in a factory, belt slippage occurs when the main shaft starts and brakes. The reason is that the main shaft load torque is large, and the ramp-up time of the drive device is set too small, which is normal after adjustment.
Optimal adjustment is a comprehensive adjustment method to systematically achieve the best match between the servo drive system and the mechanical system being dragged. The method is very simple. Use a multi-line recorder or a dual-track oscilloscope with storage function, respectively Observe the response relationship between the command and the speed feedback or current feedback. By adjusting the proportional coefficient and integral time of the speed regulator, the servo system can achieve the best working condition with high dynamic response characteristics without oscillation. In the absence of an oscilloscope or recorder on site, based on experience, adjust to make the motor vibrate, and then slowly adjust in the reverse direction until the vibration is eliminated. - 4. Spare parts replacement method: replace the faulty circuit board with a good spare part, and do the corresponding initial startup, so that the machine tool can be quickly put into normal operation, and then the broken board is repaired or repaired. This is the most commonly used troubleshooting method.
- 5. Method of improving power quality: Regulated power supply is generally used to improve power supply fluctuations. Capacitor filtering method can be used for high frequency interference, through these preventive measures to reduce the failure of the power board.
- 6. Maintenance information tracking method: Some large manufacturing companies constantly modify and improve system software or hardware based on accidental failures caused by design defects in actual work. These modifications are continuously provided to maintenance personnel in the form of maintenance information. Using this as a basis for troubleshooting, the fault can be eliminated correctly and thoroughly.
Diagnosis Method
The electrical fault diagnosis of CNC machine tools has three stages: fault detection, fault judgment, isolation and fault location. The first stage of fault detection is to test the CNC machine tool to determine whether there is a fault; the second stage is to determine the nature of the fault and isolate the faulty component or module; the third stage is to locate the fault to a replaceable module or print Circuit board to shorten repair time. In order to find the fault in the system in time, quickly determine the location of the fault and eliminate it in time, it is required that fault diagnosis should be as few and simple as possible, and the time required for fault diagnosis should be as short as possible. To this end, the following diagnostic methods can be used:
1. The intuitive method
Use the sensory organs to pay attention to various phenomena when the malfunction occurs, such as whether there is spark or bright light during the malfunction, whether there is abnormal sound, where is abnormal heating, and whether there is burning smell, etc. Carefully observe the surface condition of each printed circuit board that may fail, whether there are burnt and damage marks, to further narrow the scope of inspection, this is one of the most basic and most commonly used methods.
2. Self-diagnosis function of CNC system
Relying on the ability of the CNC system to quickly process data, multi-channel and rapid signal acquisition and processing of the error location, and then logical analysis and judgment by the diagnostic program, to determine whether the system is faulty, and to locate the fault in time. The self-diagnosis function of modern CNC system can be divided into the following two categories:
- 1) Power-on self-diagnosis Power-on self-diagnosis means that from the start of each power-on to the normal operation preparation state, the internal diagnostic program of the system is automatically executed for the CPU, memory, bus, I/O unit and other modules, printed circuit boards, CRT unit, photoelectric reader and floppy disk drive and other equipment before operating the functional test to confirm whether the main hardware of the system can work normally.
- 2) Failure message prompt When a failure occurs during the operation of the machine tool, the number and content will be displayed on the CRT display. According to the prompts, consult the relevant maintenance manual to confirm the cause of the failure and the troubleshooting method. Generally speaking, the richer the fault information prompted by the CNC machine tool diagnostic function, the more convenient it will be for fault diagnosis. However, it should be noted that some faults can directly confirm the cause of the fault according to the fault content prompt and refer to the manual; while the real cause of some faults does not match the fault content prompt, or a fault shows multiple fault causes, which requires maintenance personnel to Find out the internal connection between them and indirectly confirm the cause of the failure.
3. Data and status check
The self-diagnosis of the CNC system can not only display fault alarm information on the CRT display, but also provide machine parameter and status information in the form of multiple pages of “diagnostic address” and “diagnostic data”. Common data and status checks include parameter checking and Two kinds of interface checks.
- 1) Parameter check The machine data of CNC machine tools is an important parameter obtained after a series of tests and adjustments, and it is a guarantee for the normal operation of the machine tool. These data include gain, acceleration, contour monitoring tolerance, backlash compensation value and screw pitch compensation value. When subjected to external interference, data will be lost or chaotic, and the machine tool will not work normally.
- 2) Interface check The input/output interface signals between the CNC system and the machine tool include the input/output signals between the CNC system and the PLC, and between the PLC and the machine tool. The input/output interface diagnosis of the CNC system can display the status of all digital signals on the CRT display. Use “1” or “0” to indicate the presence or absence of the signal. Use the status display to check whether the CNC system has output the signal to the machine tool. On the machine side, whether signals such as the switch value on the machine tool side have been input to the CNC system, so that the fault can be located on the machine tool side or in the CNC system.
4. The alarm indicator shows the fault
In the CNC system of modern CNC machine tools, in addition to the above-mentioned self-diagnosis function and status display and other “software” alarms, there are also many “hardware” alarm indicators, which are distributed on the power supply, servo drive and input/output devices. The indications of these warning lights can determine the cause of the failure.
5. Spare plate replacement method
Using a spare circuit board to replace a template with a faulty point is a quick and easy way to determine the cause of the fault. It is often used in the functional modules of the CNC system, such as CRT modules, memory modules, etc. It should be noted that before replacement of the spare board, the relevant circuit should be checked to avoid damage to the good board due to a short circuit. At the same time, it should be checked whether the selector switch and jumper on the test board are consistent with the original template. Some templates should also pay attention to the template. Adjustment of the upper potentiometer. After replacing the memory board, the memory should be initialized according to the requirements of the system, otherwise the system still cannot work normally.
6. Exchange method
In CNC machine tools, there are often modules or units with the same function. By exchanging the same modules or units with each other and observing the failure transfer situation, the fault location can be quickly determined. This method is often used for fault checking of servo feed drives, and it can also be used for the interchange of the same modules in the CNC system.
7. Percussion
The CNC system is composed of various circuit boards, and each circuit board has many solder joints. Any false soldering or poor contact may cause malfunctions. When using an insulator to gently tap the circuit board, connector or electrical component with the suspected fault, if a fault occurs, the fault is likely to be at the knocked part.
8. Measurement comparison method
For the convenience of detection, the module or unit is equipped with detection terminals. Using multimeters, oscilloscopes and other instruments and meters, the level or waveform detected by these terminals can be compared with the normal value and the value at the time of the failure to analyze the cause of the failure and The location of the fault. Due to the comprehensiveness and complexity of CNC machine tools, there are many factors that cause failures. The above-mentioned fault diagnosis methods sometimes require several simultaneous applications to conduct a comprehensive analysis of the fault, and quickly diagnose the faulty part, so as to eliminate the fault. At the same time, some failure phenomena are electrical, but the cause is mechanical; conversely, it is also possible that the failure phenomenon is mechanical but the cause is electrical; or both. Therefore, its fault diagnosis can not be attributed solely to electrical or mechanical aspects, but must be integrated and considered in an all-round way.
Machine Tool Acceptance
The acceptance is generally carried out in two stages.
1. pre-validate
The purpose is to check and verify whether the machine tool can meet the user’s processing quality and productivity, and to check the information and spare parts provided by the supplier. The supplier can carry out pre-acceptance only after the machine tool passes the normal running test cutting and the production of qualified machining parts is inspected.
2. Final acceptance
According to the acceptance criteria, determine the technical indicators provided on the certificate, the acceptance work is divided into the following steps:
- (1) Unpacking inspection;
- (2) Visual inspection;
- (3) Acceptance of machine tool performance and numerical control functions;
- (4) Acceptance of CNC machine tool accuracy (including position accuracy and working accuracy).
When accepting the geometric accuracy of the machine tool, it should be completed once after the machine fine-tuning, and it is not allowed to adjust one inspection item. The position accuracy inspection shall be carried out in accordance with the corresponding accuracy acceptance standards. The working accuracy of a machine tool is a comprehensive accuracy, which not only reflects the geometric accuracy and position accuracy of the machine tool, but also includes errors caused by various factors such as the material of the test piece, the ambient temperature, the tool performance, and the cutting conditions.
In the acceptance of CNC machine tools, strengthening the inspection of the above aspects is very beneficial to equipment management and can reduce unnecessary losses.
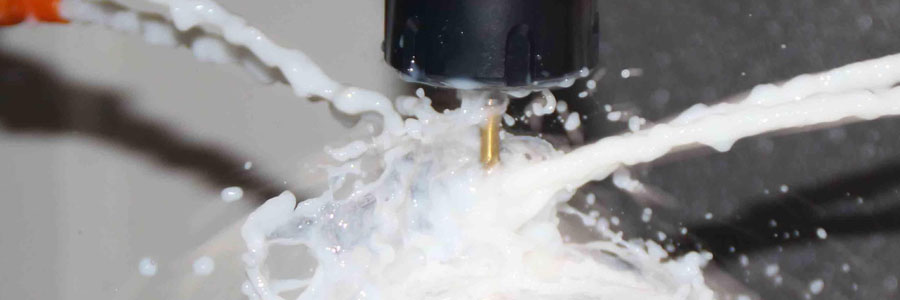
The Development History Of Cnc Machine
The Development History Of Cnc Machine
CNC machine tools were invented by American inventor John Parsons in the 20th century. With the development of electronic information technology, the world’s machine tool industry has entered the era of mechatronics with digital manufacturing technology as the core, of which CNC machine tools are one of the representative products. CNC machine tools are the processing mother machine of the manufacturing industry and the important foundation of the national economy. It provides equipment and means for all sectors of the national economy, and has unlimited economic and social effects. Industrialized countries such as Europe, the United States, and Japan have successively completed the industrialization process of CNC machine tools, while China started in the 1980s and is still in the development stage.
American Development
The U.S. government attaches great importance to the machine tool industry. The U.S. Department of Defense and other departments continue to propose the development direction and scientific research tasks of machine tools due to their military needs, and provide sufficient funds, and recruit talents from all over the world, especially focusing on “efficiency” and “innovation”. Basic research. Therefore, continuous innovation in machine tool technology, such as the development of the world’s first CNC machine tool in 1952, the creation of a machining center in 1958, the development of FMS in the early 1970s, and the first open CNC system in 1987. Since the United States first combined the needs of automobile and bearing production, fully developed a large number of automatic lines required for mass production automation, and the electronic and computer technology is the world’s leading, so its CNC machine tool host design, manufacturing and CNC system have a solid foundation and have always attached importance to it. Scientific research and innovation, so its high-performance CNC machine tool technology has been leading the world. Today’s American production of high-performance CNC machine tools used in aerospace and other industries has a lesson that it emphasizes basic scientific research and neglects applied technology. In the 1980s, the government once relaxed its guidance, resulting in a slow increase in the output of CNC machine tools. The less advanced Japan surpassed and imported a lot. Since the 1990s, the past deviations have been corrected, the technology of CNC machine tools has become practical, and the output has gradually increased.
German development
The German government has always attached importance to the important strategic position of the machine tool industry and vigorously supported it in many aspects. After the first CNC machine tool was developed in 1956, Germany paid special attention to scientific experiments, combining theory with practice, and paying equal attention to basic scientific research and applied technology scientific research. The company and the university’s scientific research department work closely to conduct in-depth research on the commonality and characteristics of CNC machine tools, and strive for excellence in quality. German CNC machine tools are of good quality and performance, advanced, practical, and genuine, and are exported all over the world. Especially large, heavy, precision CNC machine tools. Germany attaches great importance to the advanced practicality of CNC machine tools and accessories. Its mechanical, electrical, hydraulic, pneumatic, optical, cutting tools, measurement, CNC systems, and various functional components are among the best in the world in terms of quality and performance.
Japanese development
The Japanese government attaches great importance to the development of the machine tool industry, and guides the development through planning and regulations (such as “mechanical vibration law”, “mechanical and mechanical law”, “mechanical information law”, etc.). Learn from Germany on the importance of talents and machine tool components, and learn from the United States on quality management and CNC machine tool technology, and even out of blue is better than blue. Since the first CNC machine tool was developed in 1958, its output surpassed that of the United States in 1978, and its output and export volume have consistently ranked first in the world. Strategically imitate first and then create, Mr.’s mid-range CNC machine tools with large and wide output are exported in large quantities, occupying the world’s vast market. In the 1980s, it began to further strengthen scientific research and develop towards high-performance CNC machine tools.
China Development
The machine tool industry, which is the cornerstone of modern industry, is a key issue that cannot be bypassed in the process of industrial economic development. Due to innate deficiencies, China’s machine tool industry has been falling behind the mainstream level of foreign high-end machine tool projects in the development of high-end machine tools, and is now catching up. In the process.
China’s CNC machine tools are still relatively backward. China’s CNC machine tool market is huge. Compared with foreign products, China’s gap is mainly in the high-speed, high-efficiency and precision of machine tools. China is in the middle of industrialization, that is, it is gradually transforming from solving shortages to opening up to building an economic power, from poverty alleviation To become rich, a number of high-growth industries based on heavy industries, such as coal, automobiles, steel, real estate, building materials, machinery, electronics, and chemicals, have developed strongly, forming a huge demand for the machine tool market, especially CNC machine tools.
The accelerated transformation of China’s machine tool industry faces four major constraints. China’s CNC machine tool technology can only achieve five-axis linkage at most, and according to relevant sources, this five-axis is still mostly for show. Almost all of the five-axis and above are imported, and the technology of multi-point linkage is very similar to foreign technology. Big gap.
Intensified international competition in the domestic market: Due to the shrinkage of the mid-to-low-end CNC machine tool market and excess production capacity, coupled with the influx of foreign products at low prices, market competition will further intensify. As high-end products have been dependent on imports for a long time, domestic products are facing severe challenges from international competition.
The technology-leading strategy is shifting to a customer-centric strategy: economic crises often lead to large-scale industrial upgrading and enterprise transformation. The machine tool industry realizes the servitization of the manufacturing industry. The core is to be customer-centric and actively provide customers with what they need. Personalized service. Therefore, it has become the current trend to shift from simply selling products to providing overall solutions, and from being technology-centric to customer-centric.
There is a big contrast between Chinese products and Chinese market demand, and the product structure is in urgent need of rapid adjustment: Although China’s machine tool industry has maintained rapid development for many years, the phenomenon of irrational industrial and product structure still exists. The entire industry is large but not strong, and there are still a large number of high-end products. Rely on imports. Although the domestic market share of domestic machine tools has increased to a certain extent, the domestic market share of high-end CNC machine tools and core functional components is still very low, and the entire industry has a huge potential to replace imports.
The technological innovation model of enterprises needs to be improved: as the status, industrialization level and brand influence of China’s machine tool enterprises are gradually increasing, to become an industrial power, the acquisition of its technology can no longer rely on others. In the past, China has taken a path from imitation to introduction. From now on, it must take the path of independent innovation. Enterprise technology encounters a new blockade, and the establishment of an independent, new and strategic innovation model of production, education and research is the only way to support the source of technology for product structure adjustment.
China’s CNC machine tool industry will continue the momentum of structural adjustment and continue to occupy a larger market with new products and new highlights. According to the cutting method, CNC cutting machine tools can be divided into two categories: flame cutting and plasma cutting. With the continuous improvement of downstream industry demand, greater demand and higher requirements have been put forward for CNC machine tool accessories.
The development of the Northeast region is not fast, and the development of other places is also relatively slow. The third is to adjust the structure and promote the transformation to achieve results. Experts believe that in the face of the financial crisis, the majority of enterprises should continue to adjust their structure, improve quality, increase varieties and promote industrial upgrading. Coupled with the strengthening of management and lower costs, corporate efficiency has improved significantly. The decorative development trend of CNC cutting machine tools can be seen. CNC cutting machine tools are more emphasized in terms of mechanical performance, easy operation, economical price, and stable processing accuracy. Metal material processing is increasingly requiring popularization and mass production. In addition to satisfying the above-mentioned functionality, CNC cutting machine tools must also have the applicability of multiple cutting methods.
In order to improve their own strength and expand the international market faster, domestic CNC machine tool companies will adopt a variety of methods to speed up the integration with foreign companies to improve product quality and competitiveness. While continuing to develop markets in the United States, Japan and other countries, it is also fully blooming in Southeast Asia, the Middle East, Russia, Europe, and Africa. It is understood that the current operation of the metal CNC machine tool industry has the following characteristics: First, it is more difficult for export enterprises. From the point of view of enterprises above designated size, brand-name enterprises that mainly sell domestically have a relatively good momentum of development. The development of small and medium-sized enterprises without a brand is more difficult. The second is that the development of various regions is not balanced. Zhejiang, Shandong, Hebei, Beijing and Sichuan have developed relatively fast, and the private enterprises in Guangdong have also developed rapidly.
Most companies in the CNC cutting machine tool industry rely on lowering product prices to obtain the market. The consequences are low product prices, low added value, low profits, and companies do not have enough funds for sustainable development. With the development of the industry and the upgrading of competition, improving the technical content of products, owning independent patents and designs, focusing on brand building and marketing is the best choice for long-term development of an enterprise.
China’s machine tool industry has achieved sustained ultra-high-speed development in the past few years. Until the first half of 2011, demand was still strong. However, from the second half of the year, demand growth has slowed down significantly, new orders have fallen sharply, and economic benefits have gradually fallen. Increasingly severe, profit margins continue to decline.
During the “Twelfth Five-Year Plan” period, the country implemented a proactive fiscal policy and a prudent monetary policy. With technological progress, product upgrades, and the continuous advancement of national key projects and local investment projects, the level of demand for machine tool products in various industries in the national economy Will be further improved, the modernization of national defense will have more urgent demand for high-level machine tools, market demand will develop to a higher level, and the new round of market competition will become more intense.
Due to the downturn in the industry and the declining demand for machine tools by downstream manufacturing enterprises, china’s machine tool industry has been in a downturn. Upgrading and transformation has become the key word of the industry. Economical CNC machine tools have become one of the key points for the revitalization of the equipment manufacturing industry.
China’s foundry machine tool industry has made certain achievements, but its development still faces many restrictive problems. Technological innovation has always been a flaw in the domestic foundry machine tool industry. Compared with foreign foundry machine tool industry, china’s foundry machine tool industry is obviously lagging behind in the level of manufacturing technology, which makes it have obvious deficiencies in the technical level and operating speed of core operating components, product accuracy retention, and machine tool reliability. .
China’s foundry machine tool enterprises lack the awareness and ability of independent innovation and basic theoretical research, which restricts the development of china’s foundry machine tool technology. To change this situation, it is necessary to in-depth study the characteristics and requirements of the user industry’s product technology, and develop in accordance with the process characteristics To produce high-level processing equipment, at the same time, we must also pay attention to the research of basic theoretical work, so that my country’s foundry machine tool industry can develop better in the near future. The state has issued a series of policies to vigorously build emerging enterprises and high-tech enterprises. Seizing this opportunity, the enterprise has introduced a series of policies such as “adjustment and revitalization” and “independent innovation” to upgrade the machine tool technology of the enterprise and strictly guarantee the products. Quality provides a good environment and market for accelerating the development of the foundry machine tool industry.
The machine tool industry is a national basic and strategic industry. In the “Twelfth Five-Year Plan”, the independent innovation strategy has been clearly regarded as the most important component, and it has emphasized the need to use technological innovation projects to support and lead the development of the industry. The development of china’s machine tool industry must be based on independent innovation, and achieve key technological breakthroughs and industrial upgrades through independent research and development of original innovation, introduction of technology digestion, absorption and re-innovation, and integration of existing technology innovations. Construct and improve a technological innovation system that is enterprise-oriented, market-oriented, and a combination of industry, academia, research and application; insist on increasing the investment in research and development; strengthen research on key technologies and common technologies, and strive to make breakthroughs in basic and common technology research , Improve the technical level of product development.
Technological development
High speed, precision, compound, intelligence and green are the general trends in the development of CNC machine tool technology, and gratifying achievements have been made in practicality and industrialization. Mainly manifested in:
- 1. Further expansion of machine tool compound technology. With the advancement of CNC machine tool technology, compound processing technology is becoming more and more mature, including milling-turning compounding, turning-milling compounding, turning-boring-drilling-gear processing and other compounding, turning and grinding compounding, forming compounding processing, special For compound processing, the precision and efficiency of compound processing are greatly improved. The concepts of “a machine tool is a processing plant” and “one-time installation, complete processing” are being accepted by more people, and the development of compound processing machine tools is showing a diversified trend.
- 2. There are new breakthroughs in the intelligent technology of CNC machine tools, which have been more reflected in the performance of the CNC system. Such as: automatic adjustment of interference and anti-collision function, workpiece automatically exits the safe area after power failure, power-off protection function, processing part detection and automatic compensation learning function, high-precision processing part intelligent parameter selection function, automatic elimination of machine vibration during processing, etc. In the practical stage, intelligence has improved the function and quality of the machine tool.
- 3. The robot makes the flexible combination more efficient. The flexible combination of the robot and the host is widely used, which makes the flexible line more flexible, the function is further expanded, the flexible line is further shortened, and the efficiency is higher. Robots and machining centers, turning-milling compound machine tools, grinders, gear processing machine tools, tool grinders, electrical processing machine tools, sawing machines, stamping machine tools, laser cnc machine tools, water cutting machine tools and other forms of flexible units and flexible production lines have begun to be applied.
- 4. New advances in precision machining technology The machining accuracy of CNC metal cutting machine tools has been upgraded from the original silk level (0.01mm) to micron level (0.001mm), and some varieties have reached about 0.05μm. The micro-cutting and grinding of ultra-precision CNC machine tools can achieve a stable accuracy of about 0.05μm and a shape accuracy of about 0.01μm. The precision of special processing using optical, electrical, chemical and other energy sources can reach nanometer level (0.001μm). Through the optimization of machine tool structure design, super-finishing and precise assembly of machine parts, the use of high-precision full closed-loop control and temperature, vibration and other dynamic error compensation technologies to improve the geometric accuracy of machine tools, reduce form and position errors, surface roughness, etc , Thus entering the era of sub-micron and nano-level super finishing.
- 5. The performance of functional components continues to improve. Functional components continue to develop in the direction of high speed, high precision, high power and intelligence, and have achieved mature applications. Fully digital AC servo motors and driving devices, high-tech electric spindles, torque motors, linear motors, high-performance linear rolling components, high-precision spindle units and other functional components are popularized and applied, which greatly improves the technical level of CNC machine tools.
Development Issues
The domestic demand for CNC machine tools is increasing, and the development of CNC machine tools has promoted the innovation and upgrading of the functional components of CNC machine tools. The key functional component industry of China’s high-end CNC machine tools cannot meet domestic needs. The domestic CNC functional component industry mainly has the following problems.
1. Adaptability and satisfaction are far from the market demand
Judging from the current development trend of CNC machine tools in China, the adaptability and satisfaction of domestically-made functional components are far from reaching market demand. Mainly manifested in:
- 1) There is a certain gap between the product level of Chinese functional components and foreign countries. Most of the functional components produced in China are mainly labor-intensive and have low technical content, which makes it difficult to adapt to the development speed and technical requirements of domestic CNC machine tools, especially high-end CNC machine tools.
- 2) China’s functional component development capabilities are relatively weak, and the speed of new product development is slow. Most functional components need to be developed, co-produced, joint ventures, or even assembled with foreign countries. Although the situation has changed significantly in the past two years, China is still in the process of developing high-tech and latest functional components, and the market share prospects are still not optimistic.
2. The small scale of China’s CNC functional component manufacturers
According to statistics, there are more than 70 functional component manufacturers with fixed assets of more than 10 million yuan in China, accounting for less than 10% of all manufacturers. There are four kinds of “origins” in China’s functional component manufacturers: one is the enterprise developed from research institutes, colleges and universities with technical support, which can be called “institute type.” The characteristics of these enterprises are: they have a certain technological foundation and talent foundation, and have a number of technological development potentials, but the production methods are weak, it is difficult to form an industrial scale in a short time, and there are some gaps in cost, marketing, and services; The second is an enterprise that is gradually “independent” and “separated” from the main engine factory and developed mainly to produce certain functional components, which can be called the “main factory type”. These enterprises can adapt to market demand in terms of production capacity, technological level and use experience, and can form a scale to a certain extent. However, due to their inextricably linked connections with the original OEMs, they often make users doubtful in competition. Affects its market development, and at the same time, its development capabilities have certain limitations, so it is difficult to form a famous brand; third, a large number of private enterprises have emerged in Jiangsu and Zhejiang, which can be called “private enterprise type.” These companies are mainly labor-intensive and single-variety, such as chain guards, carriages, fuel injection pipes, chip conveyors, and lighting equipment. Due to the fierce competition, its quality and price can meet the market needs of medium and low-end CNC machine tools. Although these types of high-end products cannot be manufactured yet and they still need to be imported, they are largely adapted to the overall needs of the development of CNC machine tools in China. There are also some foreign joint ventures or wholly-owned enterprises that produce high-level functional components. However, the batch size is small, and there is no independent technological development capability, and it is difficult to become the main body and mainstream of functional components.
3. A large number of core components rely on imports
The development of China’s CNC machine tool industry is remarkable. In 2008, China’s CNC machine tool industry completed a total industrial output value of 3472.3 billion yuan and a product sales output value of 334.83 billion yuan, an increase of 27.5% and 26.0% respectively. From 2002 to 2008, China was the world’s largest consumer and importer of machine tools. However, behind the rapid development of the industry, a fact that cannot be ignored is that the production of key parts and components in China is still controlled by others, resulting in low profits and lack of core competitiveness in products.
4. Lack of high-tech content threatens industrial security
China’s machine tool exports have maintained a gratifying trend for years, but the embarrassment of “increasing volume and decreasing prices” directly reflects our technological level. The lack of a large number of core technologies and the dependence on key components directly affect the safety of China’s machine tool industry. Therefore, we need to strengthen the awareness of early warning work, gather the wisdom and strength of the industry, and maintain industrial safety.
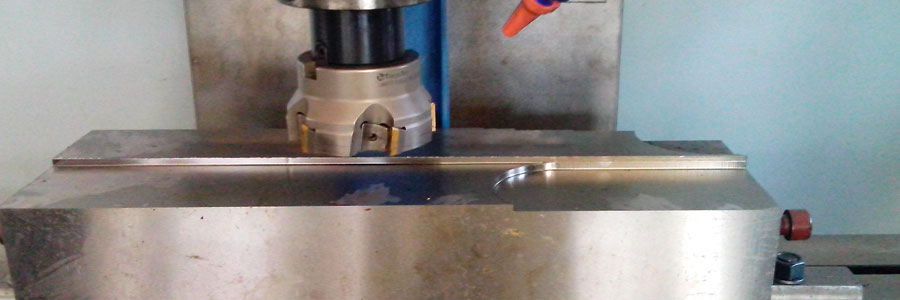
Milling Cutter Selection
Milling Cutter Selection
The indexable face milling cutter of CNC machine tools is mainly used for milling planes. When rough milling, choose a smaller diameter of the milling cutter, because the cutting force is large during rough milling, and choosing a small diameter milling cutter can reduce the cutting torque. When the CNC machine tool is used for finishing milling, the diameter of the milling cutter should be larger, and it is best to cover the entire width of the surface to be machined to improve the precision and efficiency of adding T. When the machining allowance of the machine tool is large and uneven, the tool diameter should be smaller, otherwise, the cutting quality of the workpiece will be affected due to the deep knife mark of the hanging tool.
High-speed steel end mills are mostly used for processing bosses and grooves, and are generally not used for processing the surface of the blank, because the hardened layer and sand inclusion on the surface of the blank will accelerate tool wear.
When processing the surface of the blank or roughing the hole, you can choose an end mill or corn milling cutter with cemented carbide for powerful cutting.
When machining the peripheral contour of a flat workpiece, an end mill C is often used.
In order to increase the accuracy of the groove width and reduce the number of tool changes, a milling cutter with a diameter of 7 than the groove width can be used during processing. The middle part of the groove is milled first, and then both sides of the groove are milled by the tool radius compensation function.
When processing three-dimensional curved surfaces or contours with variable bevel angles, ball end milling cutters, ring milling cutters, drum milling cutters, tapered milling cutters, disc milling cutters, etc. are often used.
When the machining allowance is small and the surface roughness requirements are high, the face milling cutter with cubic boron nitride inserts or ceramic inserts can be used to enable high-speed cutting of machine tools.
Power Requirements
As we all know, high-speed machining technology is developing rapidly, and it is the CNC machine tools that promotes this development trend. How to make good use of the performance of CNC machine tools and maintain the accuracy of the machine tools is very important.
The power supply is the energy support part that maintains the normal operation of the system. The direct result of its failure or failure is the shutdown of the system or the destruction of the entire system. In addition, some operating data, setting data and processing programs of the CNC system are generally stored in RAM memory. After the system is powered off, it is maintained by the backup battery or lithium battery of the power supply. Therefore, the downtime is relatively long, and plugging in or out of the power supply or memory may cause data loss and make the system inoperable.
At the same time, because the numerical control equipment uses a three-phase AC 380V power supply, safety is also an important part of the preliminary work of the numerical control equipment installation. Based on the above reasons, the power supply used by the numerical control equipment has the following requirements:
- The voltage fluctuation of the power grid should be controlled between +10%~-15%. However, my country’s power supply fluctuates greatly, the quality is poor, and there are hidden interferences such as high-frequency pulses, plus human factors (such as sudden opening of the gate). Power failure, etc.). During peak electricity periods, such as about an hour before going to work or leaving get off work during the day, and at night, there are often more deviations, even up to ±20%. Make the machine tool alarm and fail to work normally, and cause damage to the machine tool power system. It even leads to the loss of related parameter data. This phenomenon has occurred in CNC machining centers or turning centers and other machine tools and equipment, and the frequency is relatively high, which should be paid attention to.It is recommended to configure an AC voltage stabilized power supply system with automatic compensation and adjustment functions in workshops where Cnc Engraving Machine tools are more concentrated; a single CNC machine tool can be configured with an AC voltage stabilizer separately.
- It is recommended to connect mechanical and electrical equipment to a single power source. If it is necessary to use other power sources to supply power to certain parts of electrical equipment (such as electronic circuits, electromagnetic clutches), these power sources should be taken as much as possible from devices that form part of the mechanical electrical equipment (such as transformers, transducers, etc.). For large and complex machinery, including many machinery that work together in a coordinated manner and occupy a large space, more than one power supply may be required, which depends on the configuration of the site power supply.Unless the mechanical and electrical equipment is directly connected to the power source with a plug/socket, it is recommended that the power cord be directly connected to the power terminal of the power cut-off switch. If this is not possible, a separate terminal block should be provided for the power cord.
The handle of the power cut-off switch should be easily accessible, and should be installed between 0.6 and 1.9m above the easy-to-operate position. The upper limit is recommended to be 1.7m. In this way, the power can be cut off quickly in the event of an emergency, reducing losses and casualties. - Numerical control equipment requirements for compressed air supply system Numerical control machine tools generally use a lot of pneumatic components, so a clean and dry compressed air supply system network should be connected to the workshop. Its flow and pressure should meet the requirements. The compressed air machine should be installed far away from the CNC machine tool. According to the layout of the plant and the amount of air consumption, consideration should be given to installing refrigerated air compressors, air filters, air storage tanks, safety valves and other equipment to the compressed air supply system network.
- Numerical control equipment requirements for working environment Precision numerical control equipment generally has requirements for a constant temperature environment. Only under constant temperature conditions can the machine tool accuracy and processing degree be ensured. Generally, ordinary CNC machine tools have no specific requirements for room temperature, but a lot of practice shows that the failure rate of the CNC system greatly increases when the room temperature is too high.
A humid environment will reduce the reliability of CNC machine tools, especially in a humid environment with high acid gas, which will rust the printed circuit boards and connectors, and increase the electrical failure of the machine tool. Therefore, some users in southern China should take measures to dehumidify the environment of CNC machine tools in summer and rainy season.
- The working environment temperature should be between 0~35℃, avoid direct sunlight to the CNC machine tool, and the room should be equipped with good lighting equipment.
- In order to improve the accuracy of the processed parts and reduce the thermal deformation of the machine tool, if possible, the CNC machine tool can be installed in a relatively closed workshop with air-conditioning equipment.
- The relative humidity of the working environment should be less than 75%. The Cnc Carving Machine tool should be installed in a place away from liquid splashes and prevent the workshop from dripping and leaking.
- Keep away from the environment with excessive dust and corrosive gas
Please keep the source and address of this article for reprinting:Cnc Machine
Reprint Statement: If there are no special instructions, all articles on this site are original. Please indicate the source for reprinting.:Cnc Machine Wiki,Thanks!^^