What Is Turret Punch Presses? Cnc Turret Punching Press is the abbreviation of digital control punch, which is an automatic machine tool equipped with a program control system. The control system can logically process the program with control codes or other symbolic instructions, and decode it, so as to make the punching machine operate and process the parts.
CNC punching machine (Cnc Turret Punching Press) can be used for all kinds of metal sheet parts processing, it can automatically complete a variety of complex hole types and shallow stretch forming processing at one time, (automatically process holes of different sizes and hole distances according to requirements, or use small punches to step The punching method punches large round holes, square holes, waist-shaped holes and various shapes of curve contours, and can also be processed by special processes, such as shutters, shallow stretches, countersinks, flanged holes, ribs, embossing, etc. . Through simple Mold combination, compared with traditional stamping, it saves a lot of mold costs, can use low cost and short cycle to process small batch, diversified products, has a large processing range and processing capacity, so as to adapt to the market in time And product changes.
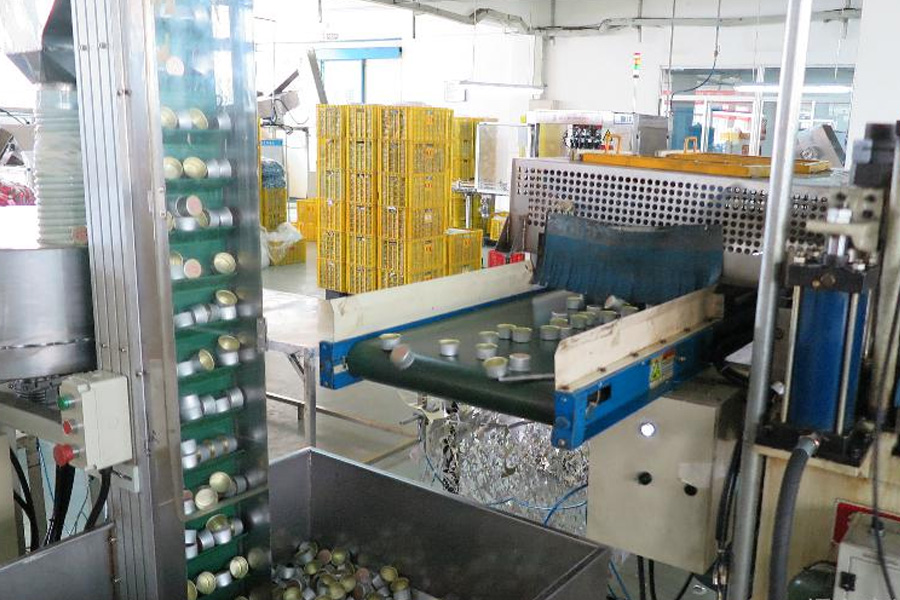
Turret Punching Press
List of Contents
The Features Of Cnc Turret Punching Press
The operation and monitoring of the CNC punching machine are all completed in this CNC unit, which is the brain of the punching cnc machine. Compared with ordinary punches, CNC punch presses have the following characteristics:
- High processing precision and stable processing quality;
- Large processing area: 1.5m*5m processing area can be completed at one time;
- Multi-coordinate linkage can be carried out, and parts with complex shapes can be processed for shear forming, etc.;
- When machining parts change, generally only need to change the numerical control program, which can save production preparation time;
- The punch itself has high precision and high rigidity, can choose favorable processing dosage, and high productivity;
- The punch press has a high degree of automation, which can reduce labor intensity;
- Easy to operate, with a certain basic computer knowledge training can be used for 2-3 days;
The Programming Process Of Cnc Turret Punching Press
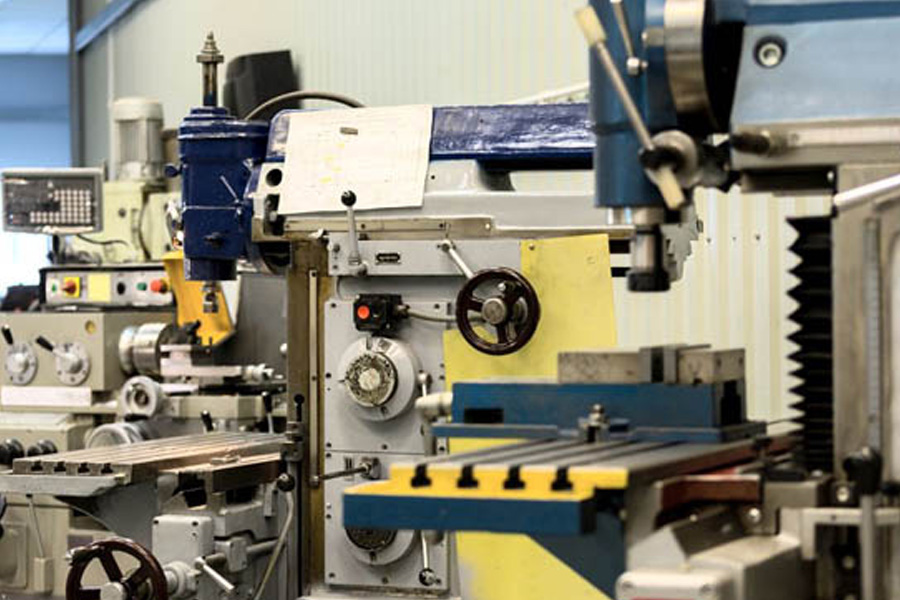
The Features Of Cnc Turret Punching Press
Input the compiled processing program into the CNC system, the specific operation method is:
Start the Cnc machine
First start the cnc machine tool through the mechanical operation panel, then input the processing program from the CRT/MDI panel, and then run the processing program.
1) Start the CNC machine tool operation
- ① Machine start button ON
- ② Program lock button OFF
2) Edit operation
- ① Choose MDI mode or EDIT mode
- ② Press (PRGRM) key
- ③ Input the program name and press the (INSRT) key after inputting the program address and program number characters.
- ④ Type in the block
- ⑤ Press the (INPUT) key after inputting the block number and operation instruction code.
3) Run program operation
- ① Program lock button ON
- ② Select automatic circulation mode
Call program operation
To call the machining program stored in the CNC system, the specific operation method is to start the CNC machine tool through the mechanical operation panel, then call the machining program in the system, and then run the program.
1) Start the CNC machine tool operation
- ① Machine start button ON
- ② Program lock button OFF
2) Call program operation
- ① Choose MDI mode or EDIT mode
- ② Press the (PRGRM) key
- ③ Call the program, and then press the (INPUT) key after inputting the program address and program number characters.
3) Run program operation
- ① Program lock button ON
- ② Select automatic circulation mode
- ③ Press the automatic cycle button
The Motion Axis Of Cnc Turret Punching Press
- X axis: the servo drive axis that moves the workpiece along the direction perpendicular to the length of the bed
- Y axis: a servo drive axis that moves the workpiece along the direction parallel to the length of the bed
- A-axis: Rotating turret-type tool magazine selects the rotation axis of the mold
- C axis: the rotating axis for automatic mold indexing, which can rotate the mold at any angle
The Processing Methods Of Cnc Turret Punching Press
- Single punching: complete punching in a single pass, including straight line distribution, circular arc distribution, circumferential distribution, and grid hole punching.
- Continuous punching in the same direction: using rectangular molds to partially overlap processing, long holes, trimming, etc. can be processed.
- Multi-direction continuous punching: the processing method of using small molds to process large holes.
- Nibble: Use a small round die to continuously punch the arc in a small step.
- Single forming: a processing method of forming a shallow stretch once according to the shape of the mold.
- Continuous forming: forming processing methods that are larger than the mold size, such as large-size shutters, rolling ribs, rolling steps and other processing methods.
- Array forming: processing multiple pieces of the same or different workpiece processing methods on a large board.
The Station Of Cnc Turret Punching Press
General thick turret molds are generally classified according to the aperture size that the mold can process to facilitate the selection of molds. It is usually divided into five gears: A, B, C, D, and E.
- A(1/2”) station: processing range Ø1.6~Ø12.7mm
- B(11/2”) station: processing range Ø12.7~Ø31.7mm
- C(2”) Station: Processing range Ø31.7~Ø50.8mm
- D(31/2”) station: processing range Ø50.8~Ø88.9mm
- E(41/2”) station: processing range Ø88.9~Ø114.3mm
The Classification Of Cnc Turret Punching Press

The Classification Of Cnc Turret Punching Press
1.Screw type
The servo operating machine uses an AC servo motor to drive the slider through the screw, and the position of the bottom dead center in the forming can be controlled by the position reading device to provide data to the position control device. Therefore, mechanical thermal expansion and elastic deformation will not affect the accuracy of the product, and the most suitable slider movement method can be adjusted and the position of the bottom dead center can be controlled in extremely small units. Therefore, it is suitable for high-precision and high-performance non-cutting forming screw-type servo presses. The hydraulic motor and energy storage are used for torque control. The position control of the bottom dead center can reach the micron level. It is a model that saves energy and has environmental protection requirements. .
2.Crankshaft Servo
A CNC punch press with a combination of a crankshaft press and an AC servo motor. This type of punching machine uses a servo motor to replace the accumulating brake and flywheel on the original punching machine. This punch has the characteristics of a servo punch that can be arbitrarily set by the slider movement method, and has the torque characteristics of a general mechanical punch. But its operating energy will not drop in the low-speed zone.
3.Double action forming
Double-action forming is a powerful method of no-cutting forming. Blocked casting in cold room casting is, for example, the intention of manipulating the plastic activity of the data by manipulating multiple punches and dies and timing diagrams. The accuracy and formability of the product can be improved, and the number of processes can even be shortened.
The double-action forming can be roughly divided into two categories: the double-action forming that focuses on the versatility of the Cnc Turret Punching Press and the use of the double-action die set; the forming of various types of production molds is simple to use the double-action punch. Recently, not only in the casting process, but also in the diversification and advancement of the composite forming of sheet metal forming and casting. Punching machines are required not only to have multiple functions, but also to have high versatility.
4.Block casting
The forming of star wheels and cross joints has been widely used in blocking casting molds and general casting punches. Its mold layout has blocking function and harmonious function. Others can save the blockage of piping during mold installation. Casting punches can be divided into two types: these functions are all in the punch and the upper and lower cylinders are on the punch and the two methods are harmoniously organized on the mold base.
5.Sheet casting
With the spread of sheet forging and forming, casting punches are required to be capable of deep drawing or shortening the number of works. Therefore, it is necessary for sliders and work tables to have oil cylinders. The original blocking casting is simply the use of high-level atmospheric pressure measures. In addition to the atmospheric pressure measures that need to be accustomed to the construction method, the sheet casting also requires sequential measures, self-locking and other functions.
6.Gear forming
Double-action hydraulic press for forming helical gears. This type of press has a total of sliding drives, 2 in the slider, 2 in the worktable, and a total of 5 drive sources are all combined with a hydraulic drive device. The early stage of forming is the same as the inner ring casting forming of the atmospheric ejector method. The male mold pierces the blocked cavity of the tooth-shaped space, and the material moves from the bottom to form the initial shape. In this state, the mold core rises, and the diameter of the mold core in the middle of the material changes from thick to thin. At this moment, there is a new space in the inner diameter of the workpiece, and new plastic activities can occur, so the tip of the tooth profile can be filled with increasing pressure data. The product processed by this method has a processing pressure of only 1300Mpa, and the collapse angle and burrs of the tooth shape are extremely small. The gear formed by using double-action forming to control the data movement can reach JIS3~4 level, which is very close to the high value-added non-cutting forming.
The Safe Operation Regulations Of Cnc Turret Punching Press
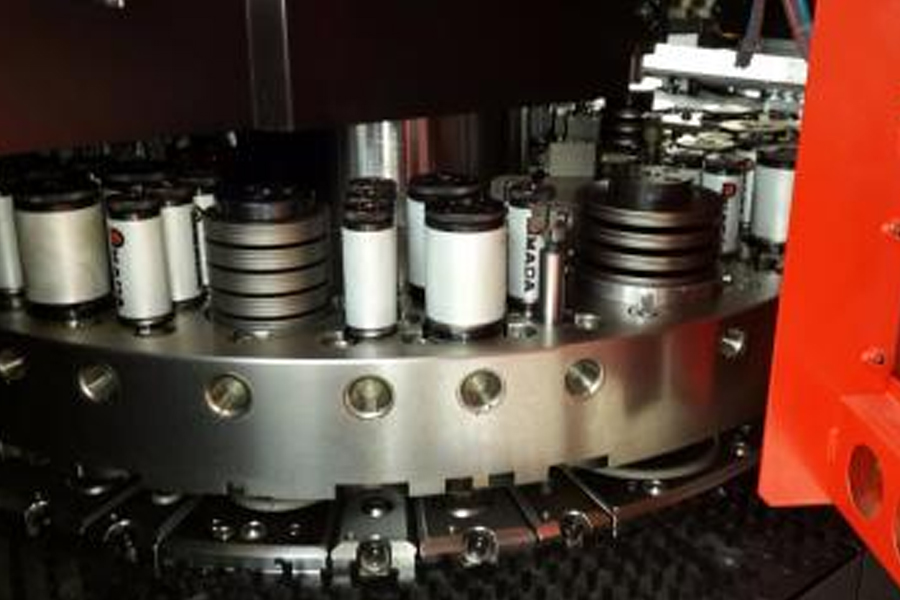
The Safe Operation Regulations Of Cnc Turret Punching Press
Punch workers must learn, master the structure and performance of the equipment, be familiar with the operating procedures and obtain operating permits before they can operate independently.
Use the safety protection and control devices on the equipment correctly, and do not dismantle them arbitrarily.
Check whether the transmission, connection, lubrication and other parts of the machine tool and the protective safety devices are normal. The screws of the mold must be firm and not moved.
The machine tool should be idling for 2-3 minutes before working. Check the flexibility of the foot brake and other control devices, and then use it after confirming that it is normal.
The mold must be firm and firm, the upper and lower molds are aligned to ensure that the position is correct, and the machine tool is moved by hand to test punch (empty) to ensure that the mold is in good condition.
Pay attention to lubrication before driving and remove all floating objects on the bed.
When the punch is taken out or when the punch is running, the operator must stand properly, keep a certain distance between his hands and head and the punch, and always pay attention to the movement of the punch, and it is strictly forbidden to chat with others.
When punching or making short and small workpieces, use special tools and do not directly feed or pick up parts by hand.
When punching or manufacturing long parts, safety racks should be set or other safety measures should be taken to avoid digging injuries.
When single punching, the hands and feet are not allowed to be placed on the hand and foot brakes, and they must be lifted (stepped) at a time to prevent accidents.
When two or more people work together, the person responsible for moving (stepping on) the gate must pay attention to the actions of the feeder. It is strictly forbidden to pick up the parts while moving (step on) the gate.
Stop in time at the end of the work, cut off the power, wipe the machine tool, and clean up the environment.
In order to ensure personal and equipment safety and prevent production accidents, please observe the following safety rules.
- Please set up a safety warning sign near the CNC punching machine.
- Please set up spacers around the CNC punch press to enclose a working area.
During the working process of the equipment, there are moving parts protruding out of the platform. If someone accidentally passes by, it may be damaged. If a partition is set up around the equipment to enclose the work area and the operator operates in a safe area, the occurrence of production accidents can be reduced. - The CNC punching machine must be managed and operated by a dedicated person (with strict training and operating qualifications).
- This equipment can only process certain plates, please do not process plates beyond the capacity of this equipment to prevent damage to the CNC punching machine.
- Before the CNC punch press starts to run, please check the equipment and its punch and mold components to ensure that each component meets the conditions for normal operation of the equipment.
- Without the permission of the manufacturer of the CNC punch press, please do not make any modifications to the equipment to avoid damage to the equipment and potential safety hazards.
The Punching Tonnage Of Cnc Turret Punching Press
According to the punching shape and material thickness, the punching force required for punching can be calculated. The following introduces the calculation method of punching force for punching core without oblique edge:
Punching force (kN) = perimeter of punch (mm) × thickness of sheet (mm) × shear strength of material (kN /m㎡)
Converted into metric tons: use kN÷9.81\
Note: The perimeter of the punch-refers to the sum of the lengths of the sides of any shape
Sheet thickness-refers to the thickness of the sheet to be punched through by the punch
The shear strength of the material-the physical properties of the board are determined by the material of the board.
The shear strength of common materials is as follows:
Material | Shear strength |
Aluminum(5052H32) | 0.1724 |
Brass | 0.2413 |
Low-carbon steel | 0.3447 |
stainless steel | 0.5171 |
For Example:
Punch holes on the 2mm thick cold plate, the shape is circle Φ25, calculate the punching force
Punch circumference=3.14×25=78.5mm
Material thickness = 2mm
Shear strength=0.3447 kN /m㎡
Punching force=78.5×2×0.3447=54.1179 kN
54.1179 kN÷9.81=5.52 metric tons
Mold Clearance
The gap between the upper mold and the lower mold is represented by the total difference. For example, when using the upper mold of Φ12 and the lower mold of Φ12.25, the gap is 0.25mm. This gap is one of the most important factors in punching. If the gap selection is inappropriate, it will shorten the life of the mold, or cause burrs, cause secondary shearing, etc., make the shape of the incision irregular, increase the demolding force, etc. Therefore, the correct selection of the gap is very important.
The gap is affected by the material. Generally, 10-20% of the plate thickness of carbon steel is the best. If there is no special requirement for the CNC turret punch press, please refer to the following table for selection:
Gap
Board thickness
|
material | ||
Carbon steel | Aluminum | stainless steel | |
0.8-1.6 | 0.15-0.2 | 0.15-0.2 | 0.15-0.3 |
1.6-2.3 | 0.2-0.3 | 0.2-0.3 | 0.3-0.4 |
2.3-3.2 | 0.3-0.4 | 0.3-0.4 | 0.4-0.6 |
3.2-4.5 | 0.4-0.6 | 0.4-0.5 | 0.6-1.0 |
4.5-6.0 | 0.6-0.9 | 0.5-0.7 |
The Maintenance Of Cnc Turret Punching Press
Test and adjust the oil volume and pressure detection function of the lubricating grease. Air system filter, oil feeder adjustment valve and other functions as well as moisture impurity test inspection and necessary adjustments. Air pressure switch setting value check and pressure detection function test and adjustment. Check the set value of the mold height indicating switch and the actual measured value. And adjustment. Check the sprocket, chain, drive shaft, worm gear and other parts of the mold height adjustment device for looseness, abnormality and chain tension. And adjustment. The upper cover of the gear box is removed, the internal parts are worn and the keys are loose, and the oil tank is cleaned. The lubricating oil CNC turret punch press is renewed and the operating conditions, noise, and vibration are tested. Drive Train
The oil volume and pressure test of the oil injection point of each part of the system. And adjustment. Test and inspection of the piston action of the brake release mechanism, the brake angle, the release brake gap and the consumption of the meter ring. And necessary adjustments.
Gap measurement and friction surface inspection between sliding guide rail and guide path, adjustment and correction if necessary. Add manual lubricating grease to flywheel bearings and check piping and joints. Test and check the operation status of the balance cylinder and the oil circuit of the oil lubrication system, joints, etc. Test and check the insulation resistance of the motor circuit and electrical operation circuit. Test the accuracy of the whole machine (perpendicularity, parallelism, comprehensive gap, etc.), adjust and correct if necessary. The appearance of the punch and the cleaning of the accessories, the inspection points and the mechanical feet (foundation) are the same as the tightening screws, the locking of the nut and the level inspection, adjust if necessary. Cleaning, maintenance and inspection of the lubricating system’s pumps, pipeline valves, etc. The air system’s pneumatic components, pipelines, etc. are cleaned, maintained, and tested and checked.
Use 3000-4000 hours to maintain the performance test of the photoelectric safety device and the test adjustment of the projection angle and the area. The appearance of another part of the electrical system, contact wear. Check and adjust the function of the same route with the emergency stop and the two-degree drop rotary cam switch box. The oil circuit of the overload protection device is cleaned, the oil chamber is cleaned, the oil is renewed, and the pressure action and function test adjustments. Check and adjust the abrasion and tension of the main motor V-belt. The parts of the brake release mechanism are disassembled and disassembled (not included in the flywheel) for cleaning, maintenance, clearance inspection, adjustment, and reassembly and debugging. The balancer, j components are disassembled and disassembled, cleaned and inspected, and assembled and re-debugged. Use 6000-8000 hours to maintain the saw tooth connecting rod, disassemble and disassemble, clean and maintain, check the tooth and connecting rod thread occlusion and wear conditions, and polish, polish the occlusal surface and apply grease. Slider assembly (ball seat, press cover. Overload hydraulic cylinder, worm gear, worm, etc.) is disassembled and disassembled, cleaned and maintained, clearance adjustment pad and wear surface, oil seal check and re-apply grease. Disassemble, decompose and clean the mold pad, check the wear surfaces, re-apply grease, and assemble and test run.
Validity period
According to the frequency of failures of CNC punch presses, the entire service life of CNC punch presses can be roughly divided into three stages, namely, the initial use failure period, the relatively stable operation period and the end of life period.
Initial use failure period
After the whole machine is installed and debugged, it starts to run for half a year to a year, and the frequency of failures is relatively high, and generally irregularities can be found.
From a mechanical point of view, during this period, although the main machine has undergone trial production run-in, due to the microscopic and macro geometrical deviations on the processed surface of the parts, the surface is still rough before the complete run-in; the parts are being assembled There are also form and position errors, which may cause large running-in wear in the initial stage of the machine tool, and cause excessive gaps between the relative moving parts of the machine tool. In addition, because the internal stress of the new concrete foundation has not yet been balanced and stabilized, the machine tool also has certain accuracy deviations. From an electrical point of view, the control system and executive components of CNC machine tools use a large number of electronic and electric devices. Although these components and devices have been strictly screened and processed by the whole machine in the manufacturing plant, in actual operation, due to alternating loads and circuits The instantaneous “surge” current of opening and closing and the impact of back electromotive force, etc., make certain components unable to withstand the initial impact, and fail due to current or voltage breakdown, causing the entire equipment to malfunction. Generally speaking, during this period, the incidence of electrical, hydraulic and pneumatic system failures is relatively high. For this reason, it is necessary to strengthen the monitoring of the machine tool, and periodically make electromechanical adjustments to the machine tool to ensure that the various operating parameters of the equipment are within the technical specifications.
Relatively stable operation period
After the equipment has experienced the aging of various electrical components in the initial stage, and after the grinding and adjustment of mechanical parts, it has entered a relatively stable period of normal operation. At this time, physical failures of various components are relatively rare, but sporadic failures are not ruled out. The occurrence of failures, therefore, during this period, we must keep a record of equipment operation for reference when troubleshooting. At the same time, it is necessary to insist on a comprehensive mechanical and electrical inspection and verification of the equipment every 6 months. During this period, the incidence of electromechanical failures is small, and most of them can be eliminated. The relatively stable operation period is longer, generally 7 to 10 years.
End of life
After the machine tool enters the end of its life, various components begin to accelerate wear and aging, and the failure rate begins to increase year by year. The nature of the failure is gradual and organic. For example, the aging of rubber parts, the wear of bushings and hydraulic cylinders, the contact sensitivity of limit switches, and the quality factors of certain electronic components have begun to decline. Most of the gradual failures are regular. During this period, we must also persist in doing well. Equipment operation records, most of the faults that occurred can be eliminated. As the CNC punching machine is a technology-intensive and knowledge-intensive equipment, its maintenance and discretion are not only conventional methods and means, but also specialized technology and testing means. When fault diagnosis is often not considered purely from the mechanical or electrical aspects, it must be comprehensively analyzed.
Please keep the source and address of this article for reprinting:Cnc Turret Punching Press
Reprint Statement: If there are no special instructions, all articles on this site are original. Please indicate the source for reprinting.:Cnc Machine Wiki,Thanks!^^