Some key parts such as the crank of the feeder are often cast. Such parts are often single-piece and small-batch. Once damaged, the outsourcing procurement construction period is long and the cost is high. The welding structure is adopted to solve the problem, which can well meet its performance. In recent years, with the development of my country’s glass industry, the glass machinery industry is also making continuous progress in the competition. According to the characteristics of users, it is generally required that the equipment parts provided are of high quality and low price, and the delivery cycle is required to be shorter and shorter, which urges our factory to pay close attention to internal management to maximize the design and development of product structure.
List of Contents
The Rise Of Feeding Machine
The crank is the key part of the feeder’s transmission and feeding, and its strength and toughness are required to be high. In the previous production, the crank blank of the feeder was generally made of casting materials, which had the advantages of certain strength, good plasticity and toughness; however, due to the high price of castings and rough appearance, especially the long production cycle of outsourcing procurement, Difficulty meeting customer needs. The use of steel plates and round steel welded structural parts, and then through a reasonable production process, can achieve the purpose of beautiful appearance, reasonable structure, material saving and time saving.
What Is Feeding Machine
Feeder is an indispensable small mechanical equipment in ceramic machining and metallurgical production. This machine consists of three parts: conveying device, host and pick-and-place manipulator.
It not only has low labor intensity, but also has accurate placement position, and makes the upper and lower planes oriented uniformly, so that the product deformation is small and uniform, the yield is high, the productivity is high, the quality of the finished product is high, and the economic cost is low.
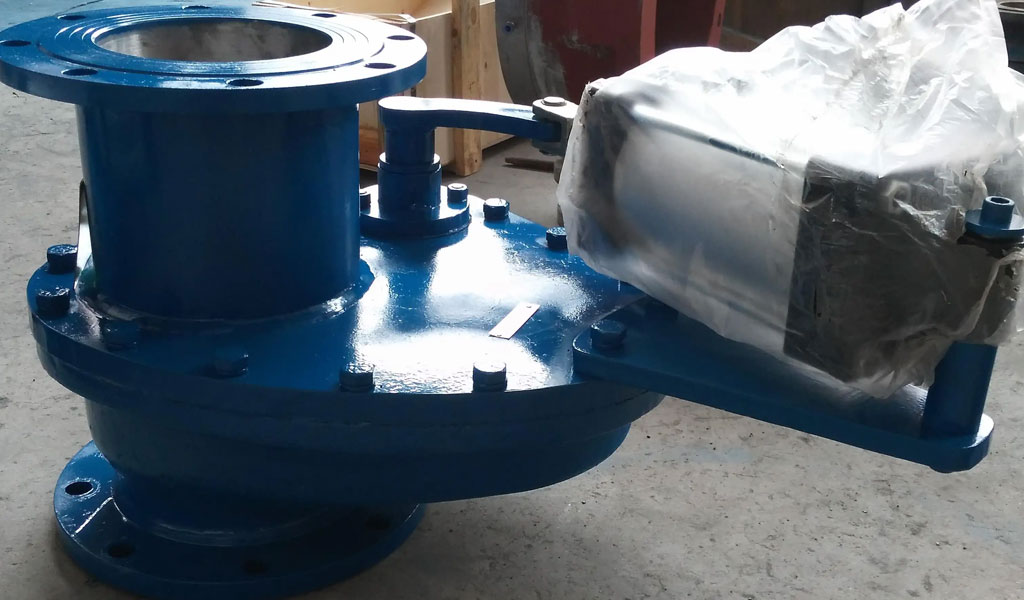
The Effect Of The Feeding Machine
Feeding the raw materials into the melting furnace is the first step in the whole smelting process, because the raw materials are sent to the Shang-temperature melting furnace with a temperature of more than 1,000 degrees. It is impossible for people to get close, and the second is that the thickness of the feeding layer and the feeding speed must be uniform, and the work cannot be completed by manpower, which requires a special equipment to complete this task. This not only saves manpower but also enables very precise and even feeding by adjusting the motion parameters of the feeder. When the product specification needs to be changed, as long as the motion parameters of the feeder are changed, the corresponding feeding amount can be accurately determined, and the operation is convenient, so it is widely used in the production of many products.
Components Of The Feeding Machine
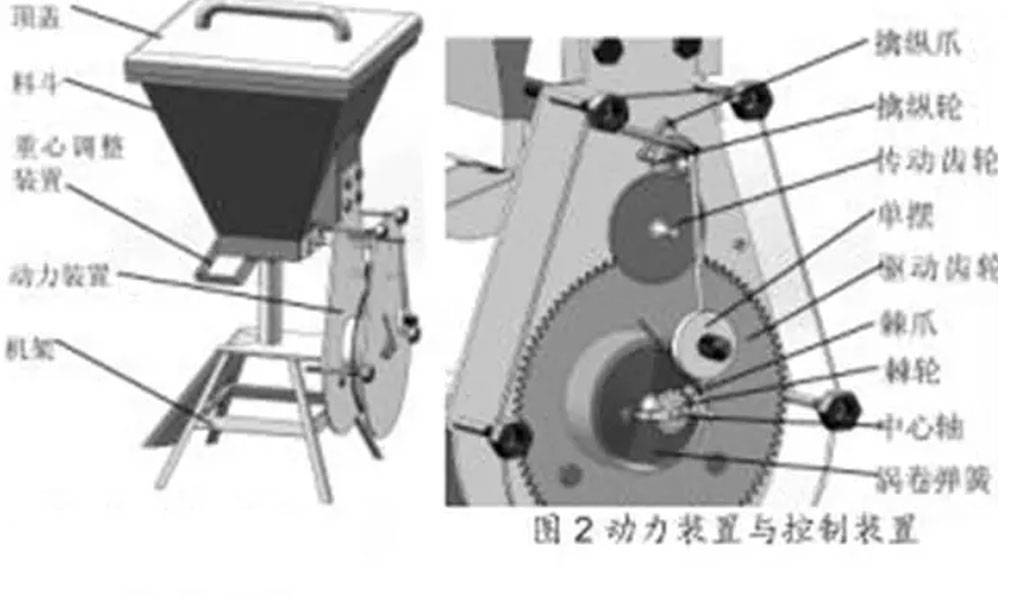
The Work Process Of Feeding Machine
In glass production, the feeding process of the feeding machine is realized by the back and forth movement of the feeding table. When the feeding table moves forward, the front of the feeding table pushes the material floating on the glass surface forward, and at the same time, the material in the silo falls by its own weight. On the feeding table, as the batching material on the feeding table slides down along the feeding table, it falls into the feeding pool in sequence from the front, and is spread on the glass surface. When the next feeding table moves forward, it is pushed into the kiln. The continuous reciprocating motion of the feeding table makes the material continuously input.
When the motor rotates, it rotates through the belt transmission mechanism, the gear box, and the drive spindle; the sprocket mechanism of the conveying device drives the speed change mechanism to operate, the speed change mechanism drives the crank rocker mechanism to operate, and the crank rocker mechanism drives the ratchet pawl mechanism, and the speed can be adjusted The adjustable ratchet and pawl mechanism drives the mud conveying roller to run, and the mud conveying roller feeds the material into the casing from the side through the belt; the material is stirred into the casing by the discontinuous blade, and then pushed forward by the continuous blade 8 to squeeze Enter the vacuum chamber, the sieve plate at the entrance of the vacuum chamber naturally forms a mud seal between the front section of the casing and the vacuum chamber. And extruded into mud strips, the air entrapped by the mud is sucked out, the discontinuous blades in the vacuum chamber grab the material squeezed through the sieve plate, and then the continuous blades push forward, pushing the material out of the machine nozzle, when the material is sent out When enough quantity is reached, the corresponding button is touched to stop feeding. Then, repeat the previous action when you need to feed again. In this way, the feeding work is completed
The Classification Of Feeding Machine
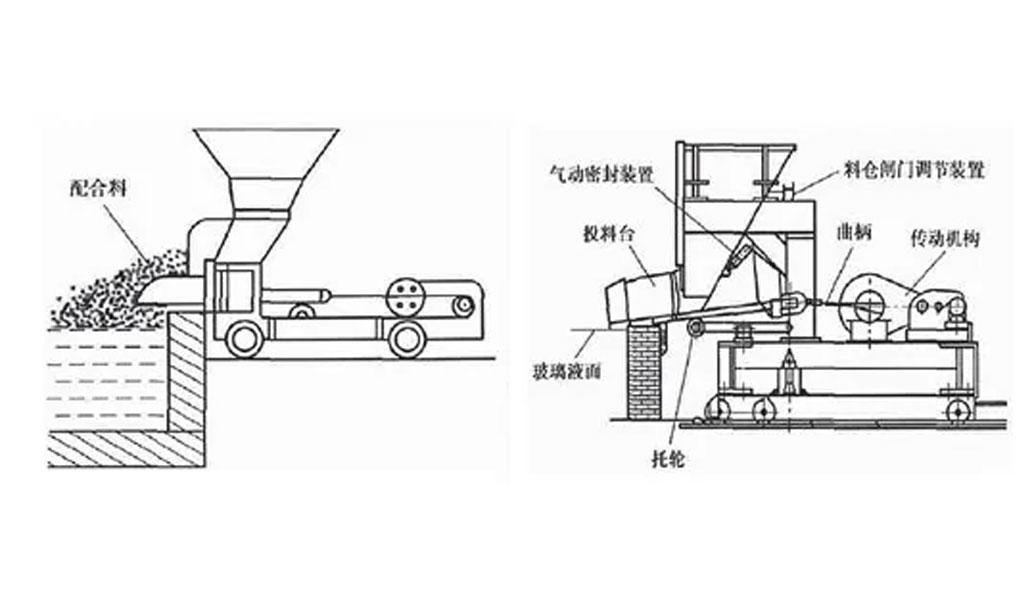
Ridge Feeder
The use of Raid Feeder has been in our company for more than 30 years. At present, it is generally still used in large and medium-sized flat glass factories in my country. Compared with other types of feeders, it also has many advantages, such as being suitable for continuous operation of glass melting capacity, and if one feeder fails, it can be replaced without affecting the normal feeding of other feeders. , The structure is relatively simple, easy to maintain, and the power consumption is also low. In contrast, the ridge feeder also has some problems, such as the large drop in feeding, uneven distribution and leakage, and the replacement of the feeder is labor-intensive. The above problems can only meet the needs of furnace feeding production through further improvement.
Inclined Blanket Feeder
The inclined blanket type feeder is a new type of gravity feeder that has been put into use in large numbers at the beginning of this century. It is mainly a circular arc oblique blanket type feeding machine. The feeding table is in a circular arc shape. It is placed on four supporting rollers through the circular drive track at the lower part of the feeding table. Its motion trajectory is an arc, hence the name. The inclination angle (approx.) of the arc tangent line at the rear of the circular arc-shaped feeding table of the circular drive inclined blanket feeding machine is much larger than that of the front ( ), and the raw materials cannot stay at the rear of the feeding table, thus fundamentally solving the problem of inclined feeding. The common leakage problem of the machine in the feeding process. Its transmission system is also improved on the basis of the inclined feeder. The length of the crank can be adjusted steplessly through the screw machine tree, so the feeding amount can be adjusted for the concentrate. The length of the connecting rod is longer than that of the inclined feeder, and the end is connected to The front part of the arc feeding table is cut with the orange arc of the feeding table, so that the feeding table can reach the best stress state. There are two ways to place the hopper of the circular arc inclined blanket feeder: one is to hang the hopper on the silo and separate it from the main body of the feeder.
The Application Of Feeding Machine
Metallurgical Steelmaking
In the steelmaking production in the metallurgical industry, the auxiliary raw material silo in the converter is generally designed according to the demand for the steel type and various auxiliary raw materials required. The basic arrangement is a material silo with a large amount of use and a large volume, and some are set as two silos, such as lime silo. However, some material silos with smaller dosage have smaller capacity, and in the production process, it is necessary to rely on the feeder to input the corresponding materials at the right time. In order to speed up the production rhythm, improve the level of steelmaking, save energy and reduce consumption; at the same time, in order to reduce manual errors, various steel mills are increasingly using automatic feeders.
Glass production
During glass production and process, the proportion of raw materials is prepared and melted in the kiln; the glass breaking liquid flows into the forming equipment to form a flat glass prototype, which is sent to the cold end through edge drawing and annealing, and is longitudinally cut, edge trimmed, cross-cut, It is completed by the process of edge breaking, vertical breaking, vertical splitting, slicing, inspection, stacking and packing. Feeding the raw materials into the melting furnace is the first step in the whole process, because the raw materials are sent to the Shang-temperature melting furnace with a temperature of more than 1,000 degrees. People can’t get close at all: the second is that the thickness of the feeding layer and the feeding speed must be uniform, and the work cannot be completed by manpower; this requires a special equipment to complete this task – a feeding machine. This not only saves manpower but also enables very precise and even feeding by adjusting the motion parameters of the feeder. When the glass specification needs to be changed, as long as the motion parameters of the feeding machine are changed, the corresponding feeding amount can be accurately determined, and the operation is convenient, so it is widely used in glass production.
Ceramic production
At present, most of the ceramic daily necessities, such as bowls and cups, are produced in large quantities and semi-mechanized by rolling forming machines. However, the feeding of the roll forming machine is mostly manual operation, which not only has high labor intensity, but also has low quality of finished products, low yield of green body and high production cost. To produce a ceramic dish with relatively small deformation, it is first required that the semi-finished product has a symmetrical uniform and small shrinkage suitable for its shape. To achieve this, it is required that the mud cake is placed in the center at the beginning of molding, and the upper and lower planes of the mud cake are correctly oriented and the size of the mud cake is appropriate. The manual feeding method requires the feeding workers to put the mud cake nervously with the rhythm of the machine, and must deal with the mud section joints at any time. The work intensity is high, and the accuracy of feeding the mud cake is relatively low, and the upper and lower planes of the mud cake cannot be considered. Orientation, so the deformation of the porcelain body is large, and the deformation is not uniform, so the yield is also low. Therefore, the feeder is also an indispensable small mechanical equipment in ceramic production.
The Outlook And Conclusion Of Feeding Machine
Because the existing feeder has shortcomings such as inaccurate measurement and slow blowing speed, an intelligent feeder design scheme based on the principle of dense phase pneumatic conveying can be proposed; on this basis, it can monitor the addition process of anti-rutting agent in real time, A set of remote monitoring system integrating data acquisition, data transmission, data processing and process early warning was designed, and the corresponding monitoring system software was built. Test results have shown that the self-developed intelligent feeder and remote monitoring system can well meet the on-site working conditions, laying a foundation for the popularization and application of this technology in engineering. For the feeding data of auxiliary raw materials, it is limited to give the name of the raw material and the feeding amount, and cannot directly correspond to each silo of the auxiliary raw material. Therefore, it is necessary to have a set of effective data distribution principles to feed the auxiliary raw materials required for steelmaking. The data is distributed, and the weight value corresponding to the type of raw material is corresponding to the actual silo, so that the control system can control the related equipment according to the corresponding silo and realize the function of automatic control.
Please keep the source and address of this article for reprinting:Feeding Machine
Reprint Statement: If there are no special instructions, all articles on this site are original. Please indicate the source for reprinting.:Cnc Machine Wiki,Thanks!^^