Turn-Mill machine tool is the fastest growing and most widely used CNC equipment among compound processing machine tools. The compounding of machine tools is one of the important directions for the development of machine tools. Compound machine tools also include Turn-Mill, turning-milling compounding, milling compounding, cutting and 3D printing compounding, cutting and ultrasonic vibration compounding, laser and stamping compounding, and many other forms. The purpose of compounding is to make a machine tool have multiple forms. Functionality, can complete multiple tasks in one clamping, improve processing efficiency and processing accuracy. The compound machine tool is a machine tool that can complete or complete the processing of multiple elements from the rough to the finished product on a host machine. Compound machine tools are generally cnc machine tools or machining centers, that is, compound cnc machine tools or compound machining centers.
Compound machine tools are the current trend of world machine tool technology development. In the general development trend of maintaining process concentration and eliminating (or reducing) the re-installation and positioning of workpieces, composite processing enables more different processing processes to be combined on one machine tool, thereby reducing machine tools and fixtures, and eliminating the need for handling between processes And storage, improve the processing accuracy of the workpiece, shorten the processing cycle and save the purpose of operating area.
This not only meets the needs of users in terms of reducing floor space, reducing parts transmission and inventory, and ensuring processing accuracy, but also meets the energy-saving and emission-reduction requirements of modern society. More and more complex parts are processed by compound machine tools, and compound machine tools have become popular products developed by machine tool manufacturers in various countries.
Compound processing is currently one of the most popular processing techniques in the world in the field of mechanical processing. It is an advanced manufacturing technology. Compound processing is the realization of several different processing techniques on one machine tool. The most widely used and most difficult compound processing is Turn-Mill processing. The Turn-Mill machining center is equivalent to a composite of a CNC lathe and a machining center.
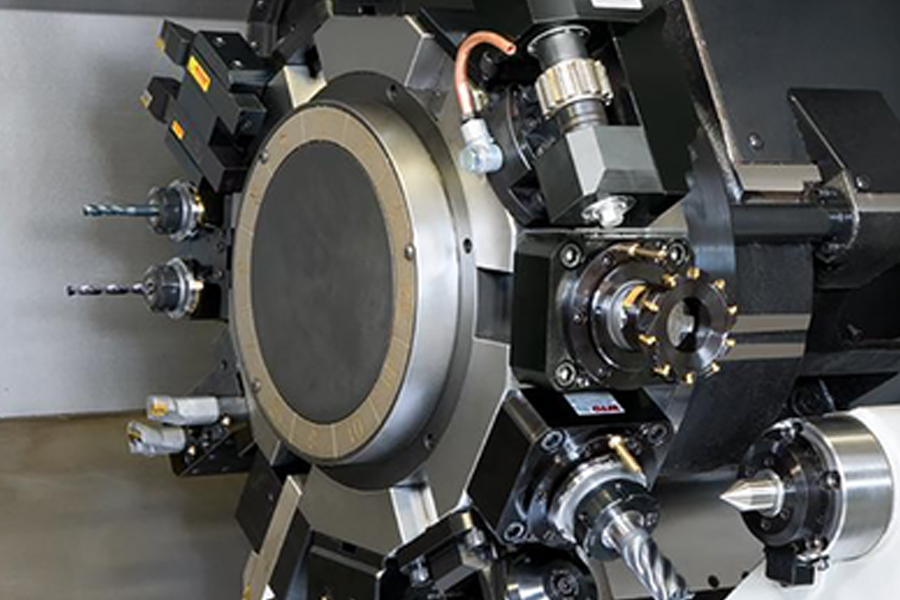
Turn-Mill Machine
List of Contents
The Advantage Of Turn-Mill Machine
Compared with conventional Cnc Machining technology, the outstanding advantages of compound machining are mainly manifested in the following aspects.
- Shorten the product manufacturing process chain and improve production efficiency. Turn-Mill processing can complete all or most of the processing procedures at one time, thus greatly shortening the product manufacturing process chain. In this way, on the one hand, the production assistance time caused by the change of the installation card is reduced, and the manufacturing cycle and waiting time of the tooling fixture are also reduced, which can significantly improve the production efficiency.
- Reduce the number of clamping and improve processing accuracy. The reduction in the number of card loading avoids the accumulation of errors due to the conversion of positioning benchmarks. At the same time, most of the Turn-Mill processing equipment has the function of online inspection, which can realize the on-site inspection and precision control of key data in the manufacturing process, thereby improving the processing accuracy of the product.
- Reduce floor space and production cost. Although the single unit price of Turn-Mill processing equipment is relatively high, it can effectively reduce the overall fixed assets due to the shortening of the manufacturing process chain and the reduction of the equipment required for the product, as well as the reduction in the number of fixtures, workshop area and equipment maintenance costs. The cost of investment, production operation and management.
The Features Of Turn-Mill Machine
- The Turn-Mill machining center uses a high-precision built-in spindle;
- Freely movable operation panel improves work efficiency;
- The models are mainly used for mass production of various small parts and complex parts for high-speed processing and diversified processing;
- Especially the slender and complicated process can be processed and formed at one time, and automatic feeding device can be configured to improve efficiency;
- Material details: cutting, copper, iron, aluminum alloy, stainless steel, Teflon and other materials [1].
The Difference Of Turn-Mill Machine
The difference between Turn-Mill machine and machining center is:
- Turn-Mill machining center is a machine tool with B-axis linkage and C-axis linkage that can do turning and milling processing. It can be said that all or most of a part can be processed on Turn-Mill machine tools, so it is also called Small production line. It can not only improve the accuracy of products and the efficiency of processing products, but also greatly save the area of the machine tool for the enterprise. In the past, it was necessary to complete the processing of one part on several machine tools. Now only one machine can complete all the parts. Processing. This type of machine tool can also be divided into vertical milling and turning compound and horizontal Turn-Mill machine tools. Such machine tools are already very common in developed countries such as Europe and Japan. China has just started and its development is very slow. This type of machine tool is still processed like the previous machine tool, which greatly wastes the Turn-Mill machine tool. The main machine tool manufacturers include WFL, DMG, MAZAK, Baomei, Mori Seiki and so on.
- For the five-axis machining center, it can only be used for milling and not for turning. Therefore, there are many limitations in processing. Turn-Mill can cover the processing of the five-axis machining center, but the five-axis cannot do the Turn-Mill processing.
The Classification Of Turn-mill Machine
Compound machine tools can be roughly divided into three categories: The first type is a compound machining machine tool with turning as the main body, such as a turning-milling compound center, a small five-axis turning-milling compound center, a turning-milling compound processing unit, etc.; the second category is a milling compound processing machine. The main compound processing machine tool, such as a five-axis bar machining center; the third category is a turning and grinding compound processing machine and an inverted turning and grinding compound center.
The advanced compound processing machine tool uses dual spindles, dual tool rests, and nine-axis control, which can realize four to five-axis linkage. The machine tool can complete all turning, milling and drilling processes in one installation.
(1) Turning-based
The compound processing machine that focuses on turning processing is a turning compound center (turn-milling center). The turning compound center is a lathe-based processing machine. In addition to turning tools, the tool post is also equipped with a milling tool that can be used for machining grooves and planes on round and rod-shaped workpieces. This type of compound processing machine often has two spindles for clamping the workpiece, which can perform the same processing on the two workpieces at the same time, or it can complete the processing of the clamping part by alternately clamping on the two spindles.
(2) Milling is the main type
The milling-based type mainly refers to the compounding of the machining center and the multi-axis of the machining center. In addition to milling, the compound machine tool (milling-turning center) based on milling-based machining centers is also equipped with a power rotary table capable of turning. The five-axis control processing machine tool, in addition to the X, Y, and Z three-axis control, in order to adapt to the change of the tool posture, each feed axis can be rotated to a specific angle position and positioned. The compound processing machine with six-axis control can simulate complex-shaped workpieces for processing.
(3) Grinding-based
The multi-axis of grinders was originally only visible on centerless grinders. Most of them were for the purpose of automating loading and unloading operations. A composite machining machine that can complete internal, external, and end surface grinding on a single machine tool was developed. For example, in Europe, a compound processing machine with integrated thread and spline grinding functions has been developed.
(4) Complex processing of different types of work
The use of compound machine tools can greatly shorten the production cycle of the workpiece and improve the machining accuracy of the workpiece. In order to improve productivity, the development and manufacturing of CNC composite machining machine tools has become a development trend of CNC machine tools. The development of composite machining technology will bring revolutionary changes to future production. The production model, production organization, and production of the factory The management will change, indicating that a complete processing era is coming, that is, the finished product is directly processed from the blank on a machine tool, and then sent to assembly and final assembly for assembly, so as to realize the real lean of no work in progress, no semi-finished products, and no finished product warehouse. produce.
Most of the turning and milling combined processing is done on the turning center, while the general turning center just replaces the ordinary turret tool post of the CNC lathe with the turret tool post with power tools, and the spindle increases the C-axis function. Due to the limitation of the turret tool post structure and dimensions, the power of the power head is small, the speed is not high, and larger tools cannot be installed. Such a turning center is mainly used for turning, and the milling and drilling functions only do some auxiliary processing. The cost of power tool post is high, which causes the cost of turning center to remain high. The domestic price is generally more than 100,000, and the imported one is more than 200,000. The average user cannot afford it. Most economical turning and milling composites are XZC axis, which is to add a rotating C axis to the chuck to realize the basic milling function.
The development of composite processing technology needs to be promoted from three aspects: one is the optimization and improvement of the design and manufacturing technology of composite processing machine tools; the second is the development of the corresponding high-performance numerical control system; the third is the improvement of the level of application technology. It should be noted that whether high-level compound machining tools such as turning-milling centers and 5-axis 5-face machining centers can successfully run in industrial production is closely related to the level of application technology, especially the programming technology in the application technology (including post-processing ), simulation inspection technology to prevent interference and collision, tool technology, etc. Some foreign companies have achieved many notable achievements in this regard.
Please keep the source and address of this article for reprinting:Turn-Mill Machine
Reprint Statement: If there are no special instructions, all articles on this site are original. Please indicate the source for reprinting.:Cnc Machine Wiki,Thanks!^^