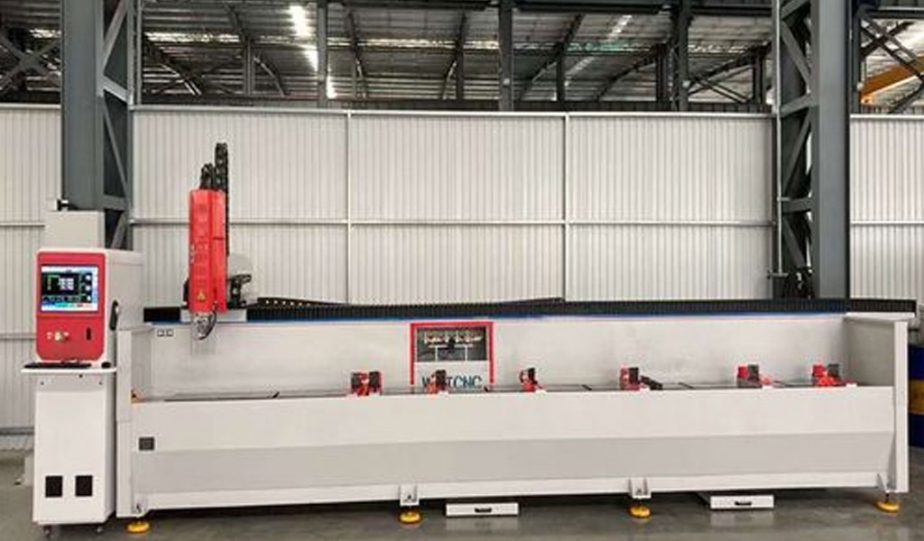
Metal Extrusion Machining center is an important method for pressure profiles machining using the principle of metal plastic forming. The metal ingot is processed into tubes, bars, T-shaped, L-shaped and other profiles at one time by extrusion. Metal extrusion press is the most important equipment to realize metal extrusion machine. The key technologies of metal extruders, including extruder frame design, force analysis and design, extruder process specification, transmission and control system, die design and manufacture, etc.
There are several different ways to classify metal extruders. According to the classification of processing materials, it can be divided into ferrous metal extruders, non-ferrous metal extruders, such as stainless steel extruders, copper extruders, aluminum extruders, alloy extruders, etc. According to the classification of processing technology, it can be divided into cold extrusion machine and hot extrusion machine. According to the classification of extrusion force, it can be divided into light extruder and heavy extruder. According to the machine mode classification, it can be divided into vertical extruder (vertical extruder) and horizontal extruder.
Metal extrusion process is a high-quality, high-efficiency, low-consumption, less chip-free machining aluminum process, which has been more and more widely used in automobile, machinery, light industry, aerospace, military, electrical and other manufacturing fields. Metal extrusion technology, as an advanced manufacturing technology, has opened up broad prospects for further research and application in the context of rising raw material prices and increasingly fierce market competition. In a sense, the degree of development of extrusion technology is an important indicator to measure the level of a country’s manufacturing industry and even the level of industrial modernization. Therefore, metal extruders have broad application prospects.
List of Contents
A brief history Of Metal Extrusion Machine
- In 1931, Germany used a mixture of graphite and mineral oil as a lubricant to successfully extrude steel pipes on a mechanical extruder. However, the use of graphite has carburizing effect at high temperature, and only carbon steel pipes can be produced, thus hindering the development of this process.
- In 1938, the French company Comptoird Etirage began to use glass lubricants as a test for hot extruded steel pipes, and obtained a patent in 1942, which was soon purchased by the United States, Britain, Japan, Spain, Austria, Germany, Sweden and other countries.
- In 1951, the world’s first steel hot extrusion workshop using glass as a lubricant was completed and put into operation in the Babcock-Wilcox Company of the United States. The extruder is a horizontal hydraulic transmission with an extrusion force of 27MN. In the following 10 to 15 years, the construction of steel hot extrusion workshop has developed rapidly. The extrusion force of the hydraulic extruder built in the early days is generally 10-20MN, and now most of it is 30-50MN, and the extrusion force of the largest hydraulic extruder has reached 100-350MN.
- In 1973, China built a 31.5MN horizontal hydraulic extruder in the Great Wall Special Steel Plant, mainly producing stainless steel pipes, thick-walled alloy structural steel pipes, and bearing steel pipes. The 16MN and 15MN horizontal hydraulic extruders designed and manufactured by China were built in the Great Wall Special Steel Plant and the Shanghai Special-shaped Steel Pipe Factory respectively in the mid-1970s to produce stainless steel pipes and carbon steel profiles and special-shaped pipes.
- In 2007, the 125MN hydraulic double-action aluminum extrusion production line was successfully developed by the China Heavy Machinery Research Institute affiliated to SINOMACH, and was successfully put into production in Liaoning Zhongwang Group.
- After Taiyuan Heavy Machinery Group successfully developed a 75MN aluminum extrusion press in 1999, it successfully developed a 75MN “short stroke” single-action horizontal aluminum extrusion press in 2003. Since then, 50MN, 36MN, 27.5MN single-action horizontal aluminum extrusion press Aluminum extrusion presses came out one after another. In 2009, the 100MN double-acting horizontal short-stroke front-loading aluminum extrusion press was successfully manufactured in Taizhong Group Corporation and delivered to Qinghai Guoxin Aluminum Alloy Pipe, Rod and Profile Co., Ltd. for use.
- In July 2009, the 36,000-ton ferrous metal vertical extruder independently developed by China North Industries Group Corporation and Tsinghua University and other scientific research institutes completed the first thermal debugging, and successfully extruded a seamless 700mm outer diameter and 200mm wall thickness. The steel pipe marks that my country’s large-diameter thick-walled seamless steel pipe manufacturing technology has broken the foreign monopoly in one fell swoop and has reached the world’s leading level.
Vertical Metal Extruder
The vertical extruder, as the name suggests, is an extruder with a vertical feeding part.
A solid step in the revitalization of China’s equipment manufacturing industry – the documentary of the world’s first 36,000-ton vertical metal extrusion machine independently developed
Xinhua News Agency, Beijing, July 27 (Xinhua News Agency reporter Zhang Yi) In midsummer, good news came from Baotou City, located in the middle of the prairie of Inner Mongolia. After nearly three years of research, the world’s first 36,000-ton ferrous metal vertical extruder independently developed by China North Industries Group Corporation North Heavy Industries Co., Ltd. successfully completed thermal debugging on July 13, and extruded the first qualified thick Wall seamless steel pipe. This move marks a major breakthrough in China’s large-diameter thick-walled seamless steel pipe manufacturing technology, and is also a solid step in China’s revitalization of the equipment manufacturing industry.
The maximum pipe diameter of the extruder can reach 1300mm, reaching the world’s leading level. It has become the earliest project among the 16 key projects in China’s equipment manufacturing industry during the “Eleventh Five-Year Plan” period, the fastest progress, the first project to be completed and put into production and achieve mass production. .
The relevant person in charge of the National Development and Reform Commission told Xinhua News Agency that large-diameter thick-walled seamless steel pipes are indispensable for supercritical and ultra-supercritical thermal power generation equipment above 600,000 kilowatts. import. After the mass production of the project, it will break the monopoly of the three major companies in the United States, Germany and Japan in one fell swoop, and save 500 million US dollars every year just by replacing imports.
The embarrassment of making a big country: half of the major equipment is imported
The equipment manufacturing industry is a basic industry that provides technical equipment for the development of the national economy and national defense construction. After more than 50 years of development, China’s equipment manufacturing industry has made remarkable achievements, and has formed an industrial system with complete categories, considerable scale and certain level, and has become an important pillar industry for China’s economic development. However, there are also problems such as weak independent innovation ability, high foreign dependence, unreasonable industrial structure and weak international competitiveness. It seriously restricts China from taking the road of new industrialization and realizing the sustainable development of the national economy.
China is known as the world’s largest manufacturing country, but half of the major equipment needed every year depends on imports. Many new automobile production lines have been built in China, of which a large number of stamping equipment, painting equipment, testing equipment, welding robots and even the entire assembly line are imported from abroad.
In order to rapidly change the status quo of China’s equipment manufacturing industry, the State Council issued the “Several Opinions on Revitalizing the Equipment Manufacturing Industry”, proposing that by 2010, a number of large-scale equipment manufacturing enterprise groups with strong competitiveness should be developed, and major equipment manufacturers with independent intellectual property rights should be strengthened. The manufacturing capacity of technical equipment basically meets the needs of energy, transportation, raw materials and other fields and national defense construction.
Among the 16 key development projects proposed by the state, the first one is large-scale clean and high-efficiency power generation equipment, including million-kilowatt nuclear power units, ultra-supercritical thermal power units, gas-steam combined cycle units, and integrated coal gasification gas-steam combined cycle units. , Large circulating fluidized bed boilers, large hydropower units and pumped storage hydropower units, large air-cooled power station units and high-power wind turbines and other new energy equipment.
In the world, only Wyman Gordon Company of the United States owns 31,500 tons of extrusion units, together with Mannesmann Company of Germany and Sumitomo Company of Japan, almost all of the world’s high-temperature and high-pressure thick-walled molding materials are monopolized. The large-diameter thick-walled seamless steel pipes required for high-power power generation equipment in China basically need to be imported.
Break the foreign monopoly, independently develop and innovate. The “36,000-ton black vertical extrusion large-diameter thick-walled seamless steel pipe project” honorably falls on NHI.
Abandoning traditional concepts: breaking through the “extreme manufacturing” problem
The manufacture of 10,000-ton heavy equipment is a sign of a country’s manufacturing capability, which involves many technical difficulties such as design, manufacture, transportation, and installation, and belongs to the field of “extreme manufacturing”. The 36,000-ton vertical extrusion press is called the “extreme manufacturing” project because of its huge project and complex system, and the first set in the world. In addition, the process tooling and personnel training are all brand-new, and unpredictable technical problems may appear at any time. In manufacturing, new technologies available to the entire industry are used on this project.
The 36,000-ton vertical extrusion press and related auxiliary equipment is a hot extrusion production line with a total of 63 sets. In the past three years, the engineering and technical personnel of NHI have overcome many major difficulties in technology, equipment, installation and debugging, and ensured that the work is carried out in a stable and orderly manner. A series of major breakthroughs have been made successively, such as wire winding, prestressed sill structure, manufacturing, installation and commissioning of super-large racks. The successful hot test on July 13 is another major progress after the manufacturing and installation of two main engines, the successful debugging of the ultra-high pressure and large flow hydraulic electronic control system, and the successful hot test of the 15,000-ton billet making machine.
Lei Bingwang, deputy general manager of China North Industries Group Corporation, who is in charge of manufacturing, told reporters that the 36,000-ton vertical extruder broke the traditional design concepts and methods of metal forging equipment, and achieved technological breakthroughs in many aspects: First, the prestressed steel wire winding structure is adopted to improve the fatigue life of the main bearing parts such as the main bearing frame and the main working cylinder of the press. The second is to adopt the prestressed sill structure to control the single weight of the parts and reduce the difficulty of manufacturing and transportation. The third is to use lower transmission to enhance the stability of the equipment. Fourth, the mature 42MPA high-flow pump is adopted, with direct transmission, simple and reliable transmission, and easy maintenance. The hydraulic transmission medium adopts mineral oil to facilitate the application of advanced pump and valve technology.
A game of chess across the country: All parties work together to overcome difficulties
With a history of more than 50 years, NHI is a large-scale backbone enterprise affiliated to China Ordnance Industry Group. The company has the capabilities of special steel smelting, investment casting and forging, heat treatment, machining, and final assembly and debugging. It has strong technical force, complete scientific research methods, and comprehensive processing. Strong ability, with national enterprise technology center and national laboratory No. 94. NHI is also the world’s largest manufacturer of 360-dwt mining vehicles. In terms of equipment manufacturing, NHI has considerable strength. In order to successfully develop the 36,000-ton vertical extruder project, NHI and Tsinghua University, which has strong scientific research capabilities in forging and pressing, have jointly launched an enterprise-school alliance.
Since the official launch of the project in 2006, in accordance with the principles of scientific planning, independent research and development, cooperation between enterprises and schools, and leading technology, with the strong support of relevant state departments, Tsinghua University, NHI, MCC Jingcheng, MCC Jingtang, Tai The heavy group pursues success together. In the whole process of project development, Tsinghua University, Yanshan University, China Forging Association, North Heavy Industries Corporation, Germany Wipco, Shenyang Heavy Forging, 447 Factory, Xizhong Institute, Taizhong Institute, Beijing Iron and Steel Design Institute, Chongqing Iron and Steel Co., Ltd. were assembled. The technology of universities and enterprises such as Design Institute, Great Wall Steel Plant, Huzhou Jiuli, Shanghai Special-shaped Steel Pipe Plant, etc., has a reliable guarantee for the successful development of the project.
The success of the project is also condensed by Shi Changxu, academician of the two academies, Yan Yongnian, Lin Feng, Guan Rendong, experts in forging and dry pressing of Tsinghua University, Zhang Yigong, an expert in rolling and forging, Wei Jun, an expert in metal extrusion, Meng Richang, Fang Yuandong, an expert in special-shaped pipes, and a process expert. Duan Sujie, oil cylinder expert Chen Weiguang and many other old, middle-aged and young experts.
Zhang Guoqing, general manager of China North Industries Group Corporation, told reporters that after the project is completed and put into operation, it will realize the localization, large-scale and industrialization of the production of large-diameter thick-walled seamless steel pipes, which will greatly reduce the production of power and petrochemical industries. It is of great significance to improve the international competitiveness of China’s equipment manufacturing industry and power and petrochemical industries. It will lay a high-end material foundation for the independent development of nuclear power, wind power, petroleum, aerospace, military industry and other industries, and will become a new economic growth point for North Heavy Industries and China North Industries Group Corporation to achieve scientific development.
Horizontal Metal Extruder
The horizontal extruder is to put down the vertical molding machine into a horizontal type, and add a blanking chamber and a pressing chamber. A pressing nozzle is installed in front of the pressing chamber, and the paste is pressed and formed by the pressing nozzle. There are horizontal extruders with fixed press chambers and rotary press chambers. Horizontal extruders with fixed press chambers are mostly used in factories.
Sectional view of a 50MN horizontal rod forward extruder without a separate perforation system. The working process of its extruder. The extruder is in the initial position and receives the heated billet 1; the extrusion cylinder 2 moves towards the front beam, so that the billet is loaded into the extrusion cylinder; the extrusion gasket is sent to the center line of the extrusion shaft with special equipment. , the ingot is located between the die seat in the extrusion cylinder and the extrusion gasket; then, the extrusion process starts, high-pressure liquid is sent to the main cylinder, the main plunger pressurizes the ingot through the extrusion shaft, and the ingot is released from the die. Extrusion in the hole; after the extrusion process is completed, the extrusion shaft retreats a little, and the lock key 5 is lifted upward; the extrusion shaft advances again, pushing out the product and the pressure, and the molding nozzle 4 moves forward to pull out the product and the pressure. ; The extrusion cylinder is withdrawn, and the gasket is taken out with the gasket clamp; the moving platform is moved to the separation shear, the product is separated from the residual pressure, the moving platform is returned, the lock key is dropped, and the new gasket is sent to the extrusion shaft again Above, the extruder returns to its original state.
Its main feature is that the movement direction of the main working parts is parallel to the ground, so it has the following characteristics:
- The extruder body and most of the auxiliary equipment can be arranged on the ground, which is conducive to monitoring, maintaining and maintaining the condition of the equipment during work;
- Various mechanisms can be arranged on the same level, which is easy to realize mechanization and automation;
- It can manufacture and install large-scale extruders, reducing construction difficulties and investment, and the specifications of the products are not limited because they are discharged at the level of the ground;
- The moving parts of the extruder, such as the plunger, the perforated beam and the extrusion cylinder, are all added to the guide sleeve and the guide rail surface, which are easy to wear and difficult to maintain accuracy. Some parts are changed due to thermal expansion. position, which can easily lead to the misalignment of the center of the extruder;
- It covers a large area. When producing pipes with a horizontal extruder, uneven wall thickness, the so-called eccentricity, is most likely to occur. This is mainly related to the disadvantages mentioned above. However, due to the advantages of the horizontal extruder, it is the most widely used in production.
According to the different uses and structures of the extruder, the horizontal extruder can be divided into a rod-type extruder and a tube-rod extruder, or called a single-action and double-action extruders. The main difference between the two is that the latter has an independent perforation system. Rod extruders are mainly used for solid-section products, but hollow ingots or composite molds can also be used to produce hollow-section products. On the tube and rod extruder, due to the independent perforation system, both solid ingots can be used to produce rods, shapes and tubes, and hollow ingots can be used to produce tubes.
The horizontal extruder can be divided into three types according to its extrusion method: forward extrusion machine, reverse extrusion machine and combined extrusion machine (which can realize forward extrusion or reverse extrusion). There is no principled difference in the basic structure between them.
The technical characteristics of the extruder mainly include: extrusion force, perforation force, stroke and speed of the extrusion rod, stroke and speed of the perforation needle and the size of the extrusion cylinder. The rated capacity of the extruder indicates the maximum extrusion force that can be given during operation, which is equal to the product of the total area of the working cylinder and the rated pressure of the working liquid. In order to reasonably use the extrusion force, extrusion speed and protect the extrusion tool from damage, the extrusion machine is equipped with a main extrusion cylinder and a secondary extrusion cylinder. When the main cylinder and the auxiliary cylinder work at the same time, the capacity of the extruder is high pressure; when only the main cylinder works, it is low pressure. The most commonly used horizontal extruder has a capacity of 8~50MN.
Aluminum Extrusion Machine – What Is Aluminum Extrusion Machine
Mainframe of aluminum extrusion machine
It can be divided into the following parts:
- Transmission and extrusion system:It is completed by the main inverter to control the frequency conversion speed regulation motor, and the transmission to the screw step by step through the gearbox distribution box and the cross splines. It cannot be changed arbitrarily.
- Heating and cooling system:It is composed of barrel heating and cooling, die heating, and screw core heating and cooling. It is controlled by the electric cavity program. It can also be manually operated according to its own experience. There is also a manual forced cooling function to control the instantaneous temperature increase.
- Automatic feeding system:It is controlled by the time relay or material level meter to transmit signal. When the material is lacking, the material level meter transmits the signal, and the system starts to feed the material. When the material supply is full, the material level meter signal is interrupted and the material supply stops.
- Feeding system:It is controlled by the frequency converter, the feeding is less, and the current and torque of the host are reduced. Otherwise, it will increase. When too much material is fed, the actual current exceeds its rated current or the torque exceeds its set value, the host will alarm and stop due to overload, generally controlled at 50%~80% of the rated value.
- Vacuum exhaust system:It is done by directly controlling the vacuum pump with a button. When the vacuum is turned on, the solenoid valve is opened, and when it is closed, the solenoid valve is closed.
Second, aluminum extrusion machine operating procedures:
- Check whether the oil pressure system leaks oil and whether the air pressure is normal.
- Check whether the conveyor belt, cooling bed and storage table are damaged or scratched.
- Before stretching, confirm the length of the aluminum profile, and then predetermine the stretching rate to determine the stretching length, that is, the moving position of the main chuck. Usually, the stretching rate of 6063T5 is 0.5%–1%, and the stretching rate of 6061 T6 is 0.8 %–1.5%.
- Confirm the clamping method according to the shape of the aluminum profile. The large-section hollow profile can be inserted into the tensile pad, but try to ensure enough clamping area.
- When the aluminum profile is cooled to below 50°C, the profile can be stretched.
- When the profile is bent and twisted at the same time, it should be corrected and twisted first and then pulled and bent.
- Test the first and second strands to confirm whether the predetermined stretch rate and clamping method are appropriate. Visually bend, twist, and check the plane clearance, flaring, and paralleling of the profile. If it is not suitable, adjust the stretch rate appropriately.
- When the normal stretch rate still cannot eliminate the bending, twisting, or the geometric dimensions cannot be qualified, the operator should be notified to stop the extrusion.
- The profiles on the cooling table can not rub against each other, collide, overlap and stack, and prevent scratching.
The working efficiency and service life of the aluminum extrusion press have a great relationship with the installation sequence of the extrusion press. Generally, the equipment foundation of the aluminum extrusion press must be able to withstand the weight of the equipment itself and the weight of the raw materials used for production. It also bears the dynamic load when the extruder is working, so the installation of the equipment must be carried out in accordance with the corresponding installation procedures.
After the extruder is installed, the process technicians should carefully read the equipment manual, and according to the requirements in the manual, formulate the process of commissioning the production of plastic products, the operating procedures for commissioning, the material plan, the tools for commissioning and the commissioning time. Understand and be familiar with the structure of the equipment and the functions of various parts, and memorize the function and usage of each button and switch.
Please keep the source and address of this article for reprinting:Metal Extrusion Machine
Reprint Statement: If there are no special instructions, all articles on this site are original. Please indicate the source for reprinting.:Cnc Machine Wiki,Thanks!^^